Infineon’s Smart Power Fab is one of the largest construction sites in Germany. What exactly does that mean, can you describe the dimensions?
Holger Hasse: It is indeed difficult to imagine the scale of the construction site if you are not on site. That’s why we’ve put together a few figures that at least give you an idea of how big it is. Our new module is being built on an area of around 30,000 m². We excavated 450,000 cubic meters of earth at the start of the project. This amount of material could fill the Frauenkirche in Dresden 18 times over. The deepest point of the excavation pit was 22 meters deep: as wide as Dresden’s Albert Bridge or as deep as some of our buildings are high. With the 13,000 meters of underground cables laid, you could easily surround New York’s Central Park.
We keep reading and hearing that construction is “on schedule”. What exactly does that mean? What work is currently being carried out and when exactly will production start?
Holger Hasse: We are keeping to the ambitious time and budget plans that we set at the start of the project. The shell of the building is now almost complete and work is already underway on installing the cleanroom roof. At the same time, the building equipment is being installed in the rooms on the lower floors. In addition, the filter ceilings and flooring are being installed in the first cleanroom sections. We are thus completing one of the largest construction sites in Germany in record time and expect to start production in 2026.
They are building right next to the ongoing and highly sensitive production of the existing modules. Even we – in the immediate vicinity – often felt the vibrations of the earthworks, especially at the beginning. How much did this affect the error rate in production and what did you have to do to ensure that the construction had as little/no impact on quality as possible?
Holger Hasse: We have installed sensors in production that measure the vibrations. These react in two stages to possible vibrations and would bring the construction site to a standstill if necessary. So far, however, the construction work has had no impact on production. The pursuit of “zero defects” is firmly anchored in all areas of our company: we constantly monitor our production processes electronically to ensure stability and achieve our zero-defect targets. Of course, we also follow this principle during the construction phase
What were the biggest hurdles during the construction period, especially when you consider the impact on local residents (space for rubble and building materials, dirt, traffic situation, noise)? What did you do to minimize the impact?
Holger Hasse: We have been implementing measures since the beginning to keep the impact of the construction site on the neighborhood and our own employees as low as possible. During the excavation phase, we deployed cleaning vehicles to clean the road. And once the residents had survived this period, we thanked them with several car wash days. We monitored the noise generated during construction on a building site to ensure that the limit values were adhered to. Another major issue is the flow of traffic. We have rented parking spaces at the airport and set up a shuttle to the construction site. Our aim is to ensure that people working on the construction site do not have to park in the surrounding area. Citizens’ dialogs were and are held regularly at the Klotzsche secondary school and at the district advisory council in Klotzsche. These events are very popular and are an integral part of our communication on the construction site.
A project like the Smart Power Fab creates jobs. According to our research and evaluations, three jobs per workplace in the Fab. To what extent are local companies and service providers involved in the construction?
Holger Hasse: Around 2,000 employees are currently working on the construction site. Together with the Dresden Chamber of Crafts and the Chamber of Industry and Commerce, we presented our construction project to local tradespeople and companies. These were then able to express their interest and will be taken into account in tenders by our general contractor. Infineon thus benefits from an excellent network of local and regional tradespeople, who in turn participate in the orders in the project.
In addition to the citizen dialogs, you provide information about the project via a regular newsletter, social media or on your website. What do you personally think everyone should know about the construction site?
Holger Hasse: With the Smart Power Fab, Infineon is making an important contribution to expanding the production base for semiconductors in Europe. A clear growth signal for Silicon Saxony. Semiconductors are crucial to solving the energy challenges of our time and shaping the green and digital transformation. Infineon is driving decarbonization and digitalization with its products. Our Smart Power Fab is set to become one of the most sustainable and environmentally friendly fabs in Europe. In doing so, we are making an important contribution to the company’s goal of achieving CO2 neutrality by 2030.
_ _ _ _ _ _
Short portrait: Project manager Holger Hasse in a video interview
Holger Hasse is a passionate manager. As project manager, he holds a key position in the largest construction project in Infineon’s history, the Smart Power Fab. His job focuses on building and equipping the clean room, which covers over 20,000 square meters. Added to this is the many times larger area for the technical infrastructure. This construction management is a balancing act: Holger Hasse’s mission is to constantly keep an eye on costs, quality and time and to take countermeasures in the event of deviations. Without his constantly growing team, the task would be impossible. In this short video interview, he talks about his activities and what drives him personally. Curious?
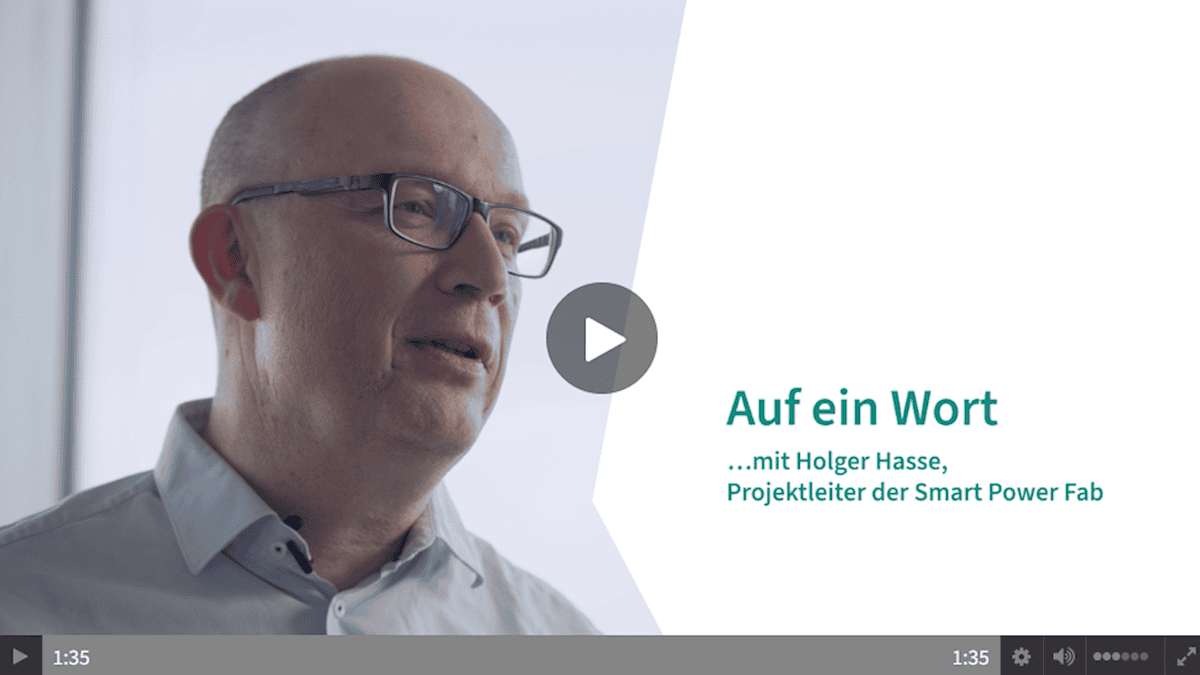
👉 To the interview
_ _ _ _ _
Sustainability at Infineon’s Smart Power Fab
Around the factory premises, Infineon has done a lot to create a species-appropriate living environment for animals. These include bat boxes and nesting aids for birds. Additional shelters and warming huts have also been created for lizards and smooth snakes. Infineon is financing these projects as part of the construction work on the Smart Power Fab. The company will also be responsible for their maintenance over the next 20 years.
Other projects include work on the Flößertgraben in the north-west of Klotzsche. Its banks are being restored to their original shape. This will provide improved living conditions for plants and animals and give the neighborhood a new place to linger. Other activities financed by Infineon included the planting of street trees along the Wilschdorfer Mühlweg and the reforestation of a wooded area in the Osterzgebirge mountains.
🌎 Reducing PFC emissions: Equipping the plants with advanced exhaust gas purification systems prevented the emission of 342,000 tons of CO2 equivalents in the 2023 financial year.
⚡Using 100% renewable electricity: electricity is generated exclusively from renewable sources.
đź’§ Industrial water consumption: The new Fab has a system that uses industrial water instead of drinking water, including a raw water storage tank with a capacity of 8,000 cubic meters – with this system we balance out peak loads in favor of the water network.
Source: LinkedIn; Infineon
_ _ _ _ _ _
🎧 Podcast Nachhaltigkeit in der Halbleiterindustrie – Zwischen Reportingpflicht und Innovationsdruck
Semiconductors enable digitalization, AI and the energy transition – but their hunger for resources is enormous: millions of liters of water every day, hundreds of chemicals, a rapidly increasing energy demand. Europe wants to achieve a 20% share of the global market. But what does this mean for our carbon footprint? Many large companies have already committed themselves to CO2 neutrality. With corresponding consequences for the supply industry and SMEs, which would not currently be required to report.
Host Julia Nitzschner takes this as an opportunity to talk to Silke Bremen (Environment, Safety & Health Manager, ESMC), RenĂ© Reichardt (Managing Director, DAS Environmental Expert GmbH) and Robert Weichert (Managing Partner, WeichertMehner) about the status quo of ESG regulation, TSMC’s ambitious sustainability goals, the pressure along the supply chain, innovation potential as well as topics that have already been addressed and challenges that still need to be solved.
🎧 listen now
_ _ _ _ _ _
Further links
👉 Infineon’s Smart Power Fab
👉 ESMC
👉 DAS Environmental Expert GmbH
👉 WeichertMehner