The past decade presented the global economy with a wide variety of challenges. From pandemics to war, everything served as a trigger for a full-blown economic crisis. Despite all the prophecies of doom, the global economic system did not collapse. One of the reasons for this was an industry that is rarely in the spotlight. Which has changed enormously in the past decade. A sector that produces nothing. But it is indispensable not only for transporting materials, components, goods and merchandise, but also for ordering them, keeping them in stock, monitoring them, and thus keeping the supply chains that are so often cited closed – logistics.
From one of the world’s leading logistics service providers (DB Schenker) to Europe’s largest semiconductor foundry (GlobalFoundries Fab 1 Dresden) to one of the world’s most modern automotive plants with a pilot effect (Volkswagen Fahrzeugwerk Zwickau), we take a look with you at current and future logistics processes, solutions and challenges. How smart is logistics already today? How differently do semiconductor and automotive companies operate in this area? There is no such thing as one logistics system that is always the same. Smart is what suits the company’s own processes and resources. From small stand-alone systems to almost human-independent process chains, we offer you technologically exciting insights and outlooks on the topic of “smart logistics”.
Logistics companies as digital pioneers
Logistics has changed enormously over the past two decades. The industry digitized in a timely, rapid and consistent manner. “In the early 2000s, the logistics sector became increasingly digital,” explains Benjamin Stein, who is responsible for sales in the Eastern region at DB Schenker. The first customers approached the German logistics giant at that time and had connections to the company’s own IT systems examined. DB Schenker reacted and made a fundamental change in the years that followed. The logistics service provider also became a digital pioneer and “supply chain manager”. A smart logistics company that not only transports, but also triggers orders for customers, monitors inventory levels, coordinates cooperation with various suppliers, manages warehouses and thus both enables production through deliveries of raw materials, materials, components, etc. and transports produced goods to customers.
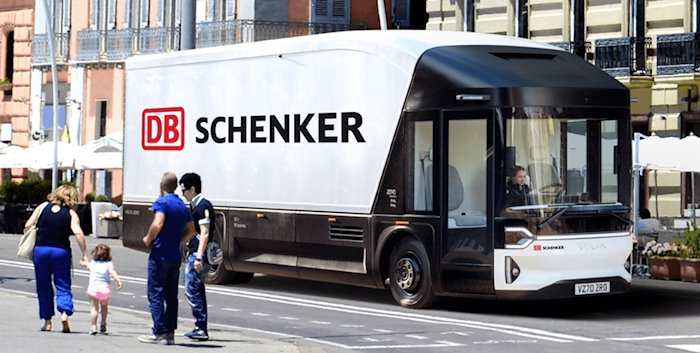
The Volta Truck from DB Schenker. | Image: DB Schenker
Apps and online access combined with countless sensors and smart systems have made not only DB Schenker’s work transparent, but also the supply chains in particular. In the meantime, tracking and tracing – i.e. the location-based tracking of freight – has become an absolute standard and is just one of many smart aspects. End-to-end digital networking of suppliers and service providers, warehouses (incidentally, in business and logistics language, the plural form for stocks of goods), producers and customers makes flows of goods and commodities not only scalable, but above all resilient. Crises and the resulting bottlenecks can be increasingly better cushioned. Each individual link in a supply chain is maximally predictable thanks to the transparency achieved.
“Today, nothing remains hidden. The data we collect and process every day guarantee the best possible logistics processes. They show which suppliers offer optimum quality and reliability. They track transport routes down to the meter. They track which transport systems are used on land, at sea or in the air, or check their efficiency. Using modern sensor technology, we even record – if the customer so wishes – the stresses to which the goods are exposed. By knowing where dangers lurk or excessive stresses occur, we can avoid them and thus transport sensitive goods – such as wafers for the semiconductor industry – safely.” (Benjamin Stein, Sales in the East Region, DB Schenker)
Countless IT systems, sensors and smart systems networked with each other
The data that logistics gathered in the past few crisis-ridden years brought about a change, and not just in logistics-heavy sectors such as the automotive industry. Increasingly, companies were once again relying on local warehouses and warehousing that was tailored to their own needs. They reviewed their relationships with suppliers. They optimized raw material, goods and freight routes. In short, the companies realigned their logistics processes on the basis of the insights and data gained. DB Schenker itself is also fine-tuning its supply chains on a daily basis to make them even faster, more reliable, more resilient and, above all, more environmentally friendly. To this end, up to 20 IT systems are interlinked in the logistics company alone. In this way, a pure transport company has become a digital group that now operates several IT locations worldwide. Empty runs, too, have been reduced to a low of one percent.
But successful digitization was far from the end of the line for DB Schenker. Already in the course of digitization, automation – from the Greek for “moving itself” – also moved into the focus of logistics. DB Schenker now operates several state-of-the-art warehouses with a degree of automation of up to 60 percent or uses state-of-the-art transport systems – some of them fully automated – for the routes to and from the warehouses. Whether automated tracking and tracing solutions for freight recording, transport robots, self-driving forklifts, automated high-bay racking systems, autonomous e-trucks, 3D printing centers or heavy-duty drones – numerous smart systems are already in use. Smart solutions such as exoskeletons, partially or fully automated order picking, or the automatic recording of delivered goods or goods to be removed from the warehouse also provide employees with the best possible physical relief. Three of the latest technological additions are particularly interesting.
Smart logistics solutions for the present and the future
Exoskeletons: Safety, prevention, quality and efficiency – the use of exoskeletons offers a variety of positive influences on work in logistics warehouses. The focus is clearly on preventive health protection: severe physical stress caused by manual load handling can be reduced with these innovative aids, thus protecting employees from overload. DB Schenker has been using exoskeletons in warehouses and goods handling in Germany since the beginning of 2022. The deployment was preceded by extensive studies and test phases (since 2019).
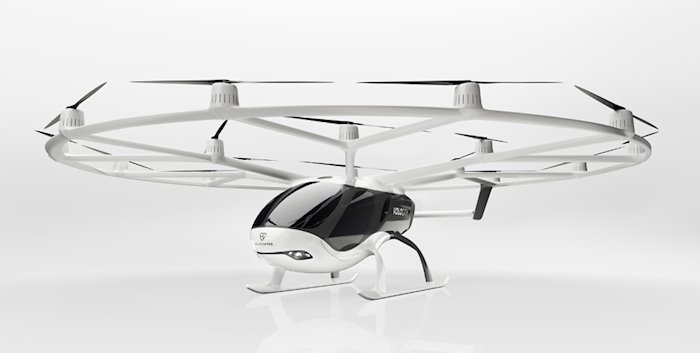
The cargo drone can transport pallets weighing up to 200 kilograms around 40 kilometers. | Image: DB Schenker
Heavy-duty drones: DB Schenker acquired a stake in the Bruchtal-based company Volocopter in 2020. Volocopter developed and produces almost 600 kilogram heavy load drones. Equipped with 18 rotors, the vertical takeoff is intended for many different missions. The all-electric cargo drone can transport pallets weighing up to 200 kilograms around 40 kilometers. This smart system is particularly suitable for transporting goods and merchandise in rural areas.
3D printing centers: 3D printing – also known as additive manufacturing – can decisively change the logistics of the future. Many questions and problems in this environment are still unresolved. In particular, data and copyright protection currently make it difficult to use this solution to avoid transport routes on a broad scale. Small and low-priced components in particular could be produced in this way where companies need them. The fear of data loss and misuse, however, still all too often makes the decision against such a solution. Nevertheless, the logistics industry is also preparing for the future in this still young business field.
The semiconductor industry – fully automated production meets hybrid logistics solution
When it comes to production, no one can fool semiconductor companies. In huge factories (also known as fabs), chips are produced on silicon wafers, sometimes even fully automatically. Even “dark fabs”, i.e. completely deserted production facilities, are already being discussed. No other industry is relying on such a high degree of automation. In the area of logistics, on the other hand, things are still more traditional. As modern as the factories of the future are in terms of production technology, and as modern and in part fully automated as the intralogistics (the transport of wafers and components within the production facilities) are, the external logistics (the connection of the fabs to service providers, suppliers and customers) still appear conventional even today. “For the extralogistics of a semiconductor plant, the focus is less on the timely provision of a wide variety of consumables and more on the way they are transported. Shock indicators on the goods and temperature control systems in the trucks, for example, are standard equipment for incoming and outgoing shipments. In addition to consumables such as gases, chemicals and, of course, wafers, the main focus is on machine spare parts. A small inconspicuous part that is not in stock can lead to very expensive production losses. Therefore, our stock includes about 20,000 spare parts of various dimensions. In order to be able to react very quickly to any ad-hoc order from the fab and at the same time remain cost-effective, we deliberately still rely on classic methods with a rather low degree of automation,” explains Katja GrĂĽnberg, Sr. Section Manager Logistics at GlobalFoundries Dresden. And for understandable reasons. Only one truck delivers the wafers needed for production each day. A total of 30 trucks a day reach Europe’s largest semiconductor plant. About ten trucks per day are available for shipping the produced wafers in particular. Compared to the automotive industry, this is hardly worth mentioning, as we will show later.
Nevertheless, GlobalFoundries’ logistics system is also in an ongoing development process. For example, the existing global Enterprise Resource Planning (ERP) system with its many evolved, site-specific stand-alone solutions is currently being replaced by a new ERP system that will highly interconnect all processes across all global sites.
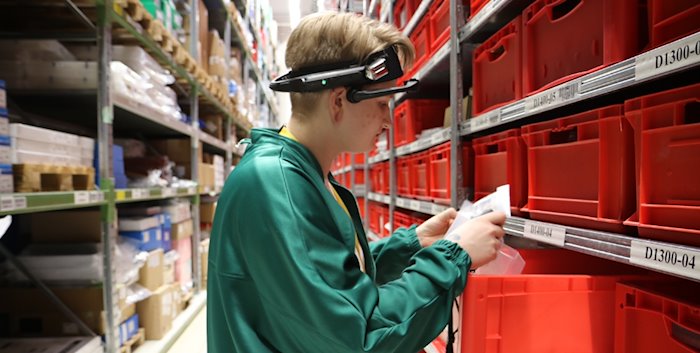
Augmented Reality (AR) Smartglasses in use at GlobalFoundries | Image: GlobalFoundries
For some time now, Fab 1 in Dresden has been using a smart system that significantly reduces the workload for employees and the environment. Together with the company TeamViewer, GlobalFoundries developed a smart virtual pick solution using augmented reality (AR) smartglasses. The AR glasses used in the microelectronics fab’s warehouses became a logistics “game changer.” Since implementing the virtual-pick solution, employees in the warehouses can work with their hands free instead of juggling tablets, bar or QR code scanners. Paper printouts as well as manual sorting and prioritizing are a thing of the past. “Employees get the information they need right where they need it. A display on their data glasses shows it directly in their field of vision,” says Katja GrĂĽnberg. This smart solution was able to generate a time saving of 25 percent in order picking. It also significantly reduced costs. The AR solution replaces around 100,000 printed pages of paper over the course of the year. Inventory accuracy has also been increased, as picking errors are now much less frequent. A complete success for GlobalFoundries. Even employees who were skeptical at first are now enthusiastic about working with the system. The conclusion is that smart, hybrid logistics can be established even with a manageable investment. Automation is not always the last word. After all, costs and benefits have to match in the logistics sector as well.
The automotive industry – individualized production meets automated logistics
A look at the automotive industry shows that the setting of priorities in both production and logistics differs from industry to industry. With a degree of automation of around 30 percent in production, automotive manufacturers such as Volkswagen are a long way from the full automation of the semiconductor sector. However, digitization and automation also meet the prevailing needs in this industry and are thoroughly optimized in terms of the cost-benefit ratio. With around 1,500 vehicles produced per day according to customer requirements, with hundreds of parts and process steps, flexibility is required at the Volkswagen plant in Zwickau. And that’s what human workers offer. Machine workers rather less so. By contrast, the logistics sector in the automotive sector is much “smarter” than in the semiconductor industry, as Volkswagen proves with its pilot plant in Zwickau. By way of comparison: if one of the world’s largest semiconductor fabs – GlobalFoundries Fab1 in Dresden – receives “only” 30 trucks per day with deliveries, with 10 trucks transporting goods and merchandise away, the Volkswagen plant in Zwickau receives 800 trucks and 25 railcars with deliveries every day. 300 trucks and up to 80 wagons transport the vehicles produced. This constant stream of vehicle parts, engines, wheels, batteries, machine parts and consumables gives an idea of how complex logistics is at one of the world’s largest automakers compared to the semiconductor industry. With a degree of logistics automation of around 30 percent, the company is currently in no way inferior to its own vehicle production.
“Our goal in logistics in the near future is a level of automation of 50 percent.”
explains Stefan Mader, responsible for logistics planning and logistics controlling at the Volkswagen plant in Zwickau. “We were the first in the world to convert our plant to the Modular E-Drive Building Kit – MEB for short,” Mader continues. The new requirements for electric vehicle production also presented new challenges for logistics. The new drive system did not allow for a “business as usual” approach. Battery logistics in particular, a heavy and hazardous goods area, made it necessary to rethink and readjust processes. “The vehicle battery of an e-car weighs just under 400 kilograms and is considered a hazardous material due to its construction. This is where people reach their limits, both due to the amount of the enormous dead weight as well as the demanding handling of the batteries to be installed.
We therefore had to develop a new, holistic logistics concept,” says Mader. A process was required that could be rolled out to all Volkswagen plants worldwide in the long term and help the entire Volkswagen company with all its brands to become CO2-neutral by 2050. It was a challenging project that was to take five years to complete.
Development of an almost fully automated logistics system for the battery sector
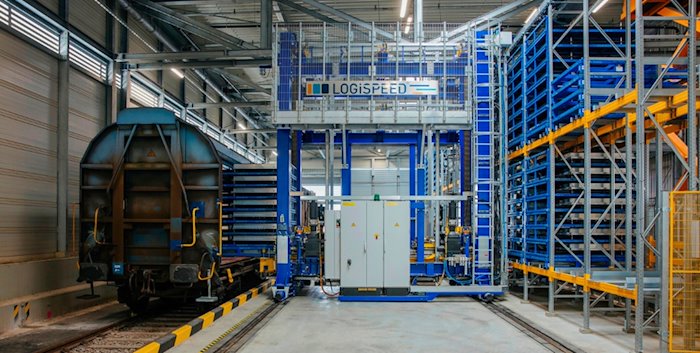
Volkswagen commissions green battery logistics for ID.3 and ID.4 | Image: Volkswagen
Since 2017, those responsible at Volkswagen’s Zwickau plant have been working on this challenge together with colleagues from the Braunschweig components site and Volkswagen Group Logistics. The cell modules are assembled into battery systems in Braunschweig, which are then installed in Zwickau. A completely new logistics process has been created that links the cell module supplier, battery assembly and the vehicle manufacturing plant in a kind of circuit – and does so almost fully automatically. The process uses newly designed transport racks that can be used for modules and systems alike – in trains and trucks. In the meantime, this process has matured. “Only two employees are still involved. The train driver, who transfers the cell modules from the supplier to the battery assembly and manufactured batteries to the vehicle plant, and the e-truck driver, who transports the batteries to the vehicle plant,” says Stefan Mader proudly.
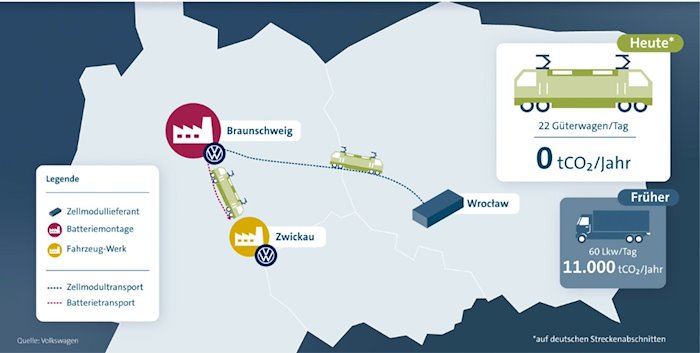
The green supply chain for e-car batteries. | Image: Volkswagen
The train alone now replaces the commute of 35 trucks between the Braunschweig and Zwickau sites and can replace up to 45 trucks at peak times. This not only relieves the strain on the road infrastructure, but also on the environment thanks to greatly reduced CO2 emissions compared with conventional truck transport. And the e-trucks, MAN models converted as part of a development project and used in internal plant transport between battery landing and assembly, are also helping Volkswagen to achieve the climate targets set by the company. All loading and unloading operations for rail cars and e-trucks (from the first mile to the last), storage of the battery systems and battery sequencing are fully automated. Finally, the batteries are moved to the assembly line in the plants using conveyor technology. The entire process is “copy-ready” and can therefore already be rolled out to all Volkswagen plants worldwide. Even the further use of disused cell modules (“Second Life”) in driverless transport systems and the recycling of battery systems have already been thought out and planned for.
Conclusion
There is no such thing as smart logistics. On the contrary, logistics is constantly changing, constantly producing new solutions and processes that help to save costs, resources or time. Small and medium-sized enterprises (SMEs) in particular can benefit enormously from this toolbox of possibilities. It is also worth taking a look behind the scenes in other industries to find the options that really suit your own company. It is not always necessary to digitize or automate entire process chains to make smart logistics a reality. Often, even small, already existing stand-alone solutions help to take a big step toward your own company’s goals. If in doubt, seek out exchanges with experienced logistics companies, join a network like Silicon Saxony, or get in touch with industries with similar challenges to yours. In this way, you too can find the right smart logistics for your company.
_ _ _ _ _
Further Links
👉 DB Schenker website
👉 Volkswagen website
👉 GlobalFoundries