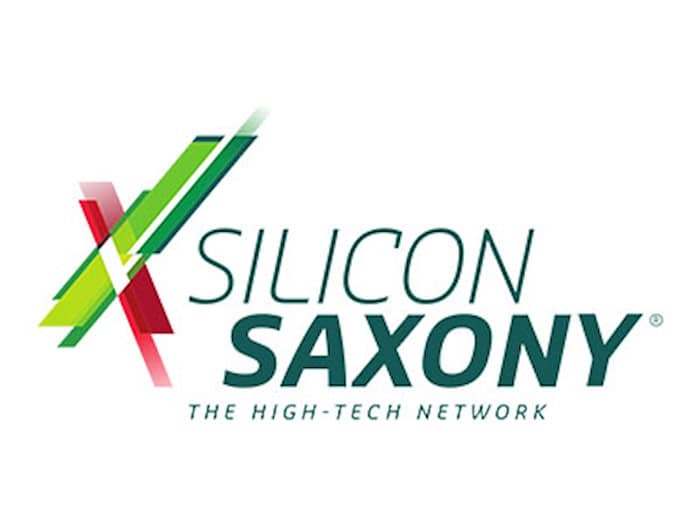
Silicon Saxony is the European location for the microelectronics industry. Every third chip produced in Europe is manufactured here. With Robert Bosch Semiconductor Manufacturing, Infineon, GlobalFoundries, X-FAB and SAW Components, there are already five established semiconductor plants – so-called fabs – in the Free State of Saxony, more precisely in its capital Dresden. Each of these fabs is different in size, design and age. The sixth and seventh fabs at the site are currently under construction with the new €10 billion building by esmc (European Semiconductor Manufacturing Company) – a consortium of TSMC, Bosch, Infineon and NXP – and the new Jenoptik plant.
A fab within a fab – supply and disposal as core topics of the sub-fab
Despite their differences, all semiconductor plants have one thing in common: namely the sometimes more, sometimes less large machine, plant and supply park, which is largely concealed and makes the actual production of microchips in clean rooms possible in the first place – the so-called sub-fab. As its name suggests, the sub-fab is located below the actual semiconductor production line. It supplies the systems and machines used in chip production with everything they need – from fresh and cooling water to chemicals and electricity. Last but not least, the sub-fab also disposes of all the substances and materials generated during semiconductor production – from waste water and chemicals to exhaust gases. While the view into the clean rooms of highly automated microelectronics production is probably familiar to many people by now, most people have never heard, read or seen anything about the sub-fab.
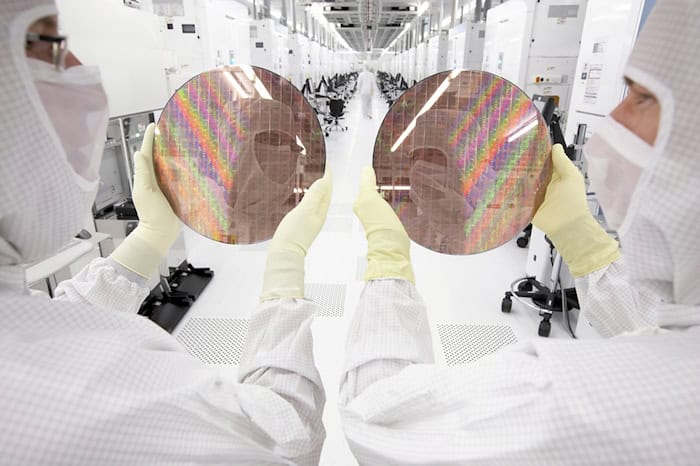
View of the GlobalFoundries Dresden fab. Photo: GlobalFoundries
The sub-fab – a planning challenge with thousands of lines and machines
Efficiently linking the sub-fab supply level with the actual production level is a masterpiece of planning. Only a few highly paid specialists worldwide are able to do this. This is because, unlike on the production level, the most diverse media, hazardous substances and resources come together here in the smallest of spaces. In some cases, more than 3,000 pumps, 2,000 exhaust systems and thousands of coolers, supply and power lines must be planned and ultimately positioned in such a way that they do not influence or even endanger each other, while still optimally supplying the production machinery one floor above. A wide variety of chemicals, electricity, waste gas, process and ultrapure water, burners and coolers have to be positioned in the best possible way on just a few square meters. Once this planning challenge had been overcome in the past, the internal fab focus usually shifted to the high-purity production area above. The majority of the sub-fab’s utilities, machines and systems then ran at full capacity 24 hours a day, seven days a week. Service and repairs alone ensured minimal interruptions and occasional downtime.
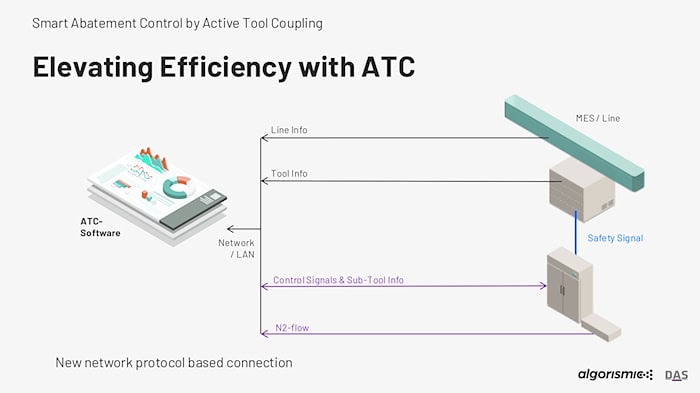
Visualization of the Subfab 360 ATC solution. Image: algorismic
Environmental requirements meet sustainability goals – “dimming” machines with software
In times of climate change, environmental social governance (ESG) and the overarching concept of sustainability and environmental protection, this approach now seems outdated. Increasingly, the question arises as to how the highest environmental requirements can be met and how important resources such as water, electricity or chemicals can be saved in the fabs and thus also in the sub-fab. “Depending on the age and design of the fabs, the sub-fab’s machinery and equipment varies greatly. Burners, coolers, pumps and suppliers from a wide range of manufacturers and years of manufacture must be actively controlled or flexibly “dimmed” in order to effectively save resources. This is a difficult task, especially in older fabs. This is because it requires access to various communication protocols from a wide range of machines and systems, and it is necessary to reconcile the requirements of production with the resulting requirements in the sub-fab,” explains Stefanie Hammer, Managing Director of the Dresden-based software start-up algorismic. Stefanie Hammer and her team successfully rose to this challenge. The start-up now offers the world’s first manufacturer-independent open source software, which can be used to control almost all machines and systems in the sub-fab flexibly and in a resource-saving manner, or to adapt them without technical retrofitting and the associated downtime. To do this, the software compares the data from production with data from the machines and systems in the sub-fab and regulates the latter as required.
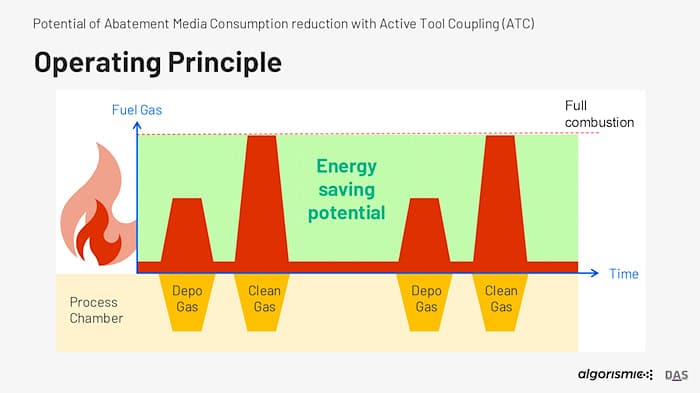
Graphic showing the savings potential of the Subfab 360 ATC solution. Image: algorismic
A development by ADG Automatisierung Dresden GmbH becomes a game changer
The open source software solution “Subfab 360 ATC” offered by algorismic worldwide is based on control software for systems and machines developed by ADG Automatisierung Dresden GmbH – a Silicon Saxony member. ADG presented this highly interesting product to DAS Environmental Expert GmbH (DAS) – also a Silicon Saxony member – a few years ago. Stefanie Hammer, then still an employee at DAS and an experienced semiconductor and sub-fab specialist, recognized the potential of this solution – including for DAS products and solutions and for the systems and machines of DAS customers in general. The initial negotiations between Hammer and ADG were very promising. In the end, only an intensive functional test and a look at the code of the software solution stood in the way of a takeover. Other members of Silicon Saxony were on hand to support the start-up. As a first step, Stefanie Hammer approached DevBoost GmbH, an experienced software company in the region, and had the open source software offered for sale put through its paces. The DevBoost team specializes in the analysis, evaluation and systematic further development of existing products and development processes of software manufacturers and was thus able to contribute the appropriate know-how for this assignment.
Silicon Saxony companies support the startup algorismic in the software assessment
“Our task was to intensively analyse the software solution of ADG Automatisierung Dresden GmbH. This included quality criteria for the architecture, the software code and the way in which system functionalities are developed, tested and documented. Were established software development standards adhered to? Are there any hidden risks in the software system, e.g. do major investments need to be made to ensure security or functionality? Which technologies were used and how complex will future adaptations be?” says Dr. Tobias Nestler, Managing Director of DevBoost GmbH, outlining the contents of the quality check. The necessary findings were compiled and discussed in the form of questionnaires, code reviews and joint workshop sessions. The results of the technical analysis were delivered quickly and painted a consistently positive picture. Stefanie Hammer received the desired confirmation to continue on the path she had chosen. Only one last long-term test of the software solution still had to be organized in one of the local sub-fabs. And here, too, they quickly found what they were looking for in the Silicon Saxony network. One of the six semiconductor companies active at the Dresden site agreed to test the solution under live conditions. This was to begin in 2022 on two process systems – an etcher and a furnace – with sub-fab devices and deliver remarkable results by the end of 2023.
Field study confirms the capabilities of the solution and reveals enormous savings potential
Fuel gas, electricity, compressed air, caustic, cooling water and fresh water – the two machines controlled with the new software solution from algorismic and based on current production data reduced their consumption by up to 68 percent. Both systems have been running continuously since 2022 without any problems. This has reduced operating costs and significantly increased resource and energy efficiency. The new software solution from algorismic also provides valuable insights into the consumption of the sub-fab and its individual components. algorismic is now also a member of Silicon Saxony and presented its software solution to a wide audience at Silicon Saxony Day, SEMICON Taiwan and SEMICON Europe in Munich, among other events.
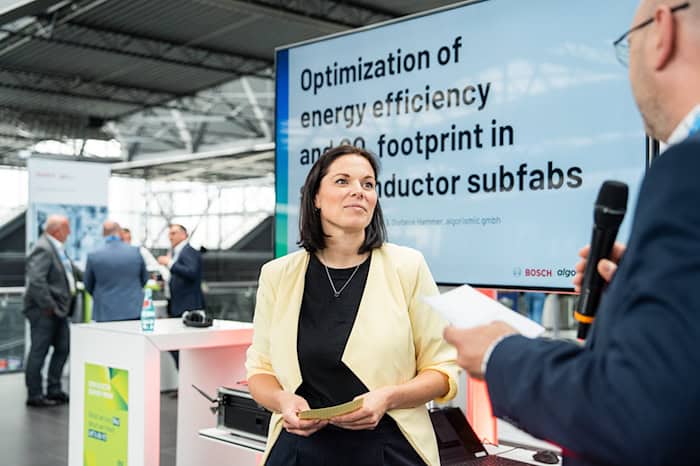
Presentation by Stefanie Hammer, Managing Director of algorismic, during Silicon Saxony Day 2024. Photo: Tommy Halfter
algorismic is expanding its own database and integrating almost all Sub-Fab components
To date, Stefanie Hammer has presented her “Subfab360 ATC” solution to all of the world’s major semiconductor manufacturers. Flexibly configurable and integrable, it offers sub-fabs of all sizes and ages a sustainable and resource-saving alternative for modernizing their plant and machinery. “We have now expanded our team and strengthened it with experienced software specialists and in the area of project management. Thanks to the support of our network partners ADG Automatisierung Dresden, DAS Environmental Experts, DevBoost and the large semiconductor manufacturer, we have succeeded in providing a reliable, manufacturer-independent and highly efficient machine and plant control system that enables significant savings in every sub-fab and finally brings transparency to this previous “blind spot” of semiconductor plants. With minimal effort and cost, we can integrate all sub-fab components into our solution or have already done so thanks to our constantly growing database. From a few dozen to a few thousand machines and systems, sub-fabs of any size and age can now be operated more sustainably and with fewer resources.
This makes algorismic an outstanding example of how cooperation between a wide range of companies and fields of expertise in a cluster like Silicon Saxony can bring excellent solutions to light. When start-ups, small, medium-sized and large companies work together and the fields of microelectronics, software and mechanical and plant engineering support each other, innovations are created that change things for the better worldwide. Resource savings of up to 68% not only make microelectronics more cost-efficient, but also more environmentally friendly and sustainable. This is good news for an industry such as semiconductors, which not only sees itself as a key industry in the field of sustainability, but is also constantly striving to make its own production even more energy and resource efficient. Dresden is once again living up to its role as an important microelectronics and innovation location. The realization is that a lot can be achieved together. Because “Teamwork makes the dream work”.
– – – – – –
In future, our new “Network in the Spotlight” series will provide insights into collaborations, partnerships and co-innovation processes, highlighting the joint development of exciting and innovative products, services and solutions in Silicon Saxony.
Are you also part of a joint or co-innovation project? Then send us an email to redaktion@silicon-saxony.de or contact our editor Robert KrauĂźe by phone (+49 351 8973-3866). Together we will publish your network story.
– – – – – –
Further links
👉 www.algorismic.com
👉 Subfab360 ATC
👉 www.das-ee.com
👉 https://devboost.com/
Photos and images: algorismic and Tommy Halfter (Silicon Saxony Day)