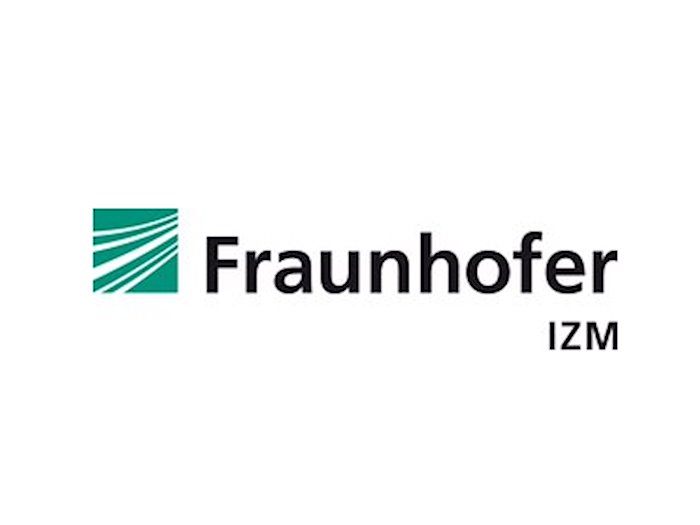
In order for electronic components to work undisturbed by moisture, they need a protective housing that keeps them away from the sensitive components wherever possible. This is the only way to ensure a long service life, for example in engines in cars or large industrial machines. Depending on the application, the housings must be designed to withstand different environmental influences and changing climatic conditions. This is because microclimates can form inside them due to an internal temperature distribution resulting from the power dissipation of the corresponding electronic assemblies. By carefully placing the sensitive components, a functioning electronic system can be created in which the microclimate in the housing is locally favorable for the application of the electronics.
The fact that the climatic conditions in a sealed housing are not constant depending on operation has now been demonstrated in the successfully completed RoDosH project (Relevance of Diffusion of Humidity in sealed Housings) using the example of a photovoltaic inverter housing from the company SMA. An inverter converts the captured solar energy in a solar module so that it can be fed into the power grid. The Environmental & Reliability Engineering department at the Fraunhofer Institute for Reliability and Microintegration IZM, which has been conducting reliability simulations and assessments for 30 years, used its methodological expertise to study the inverter housing in four process steps. The special feature here is the diversity of expertise of the researchers. In order to be able to characterize and simulate materials in detail, as well as to be able to exchange information with colleagues from the institute’s own production, many years of experience from various research and industrial projects are required, which Fraunhofer IZM and its working groups bring to the table. In addition to the large number of use cases that the researchers* have incorporated from previous work, they have the most modern equipment at their disposal – from classic climate chambers to special drop test machines and special measuring devices, such as a so-called TGA-SA, which is the same as thermograviation with sorption analyzer.
Characterization and modeling of sealing concepts
Ahead of the classic but also more specific reliability tests, the first step at Fraunhofer IZM is almost always load profiles or mission profiles. In this case, two load profiles were derived for the photovoltaic inverter’s housing, detailing the climatic conditions to which housings of this type are exposed in various locations around the world. The experts from Berlin implemented a profile under harsh climatic conditions, e.g. photovoltaic devices from Kuala Lumpur and Mumbai, by analyzing and outlining available weather data from the Internet, such as very high average temperatures and high humidity. In parallel, they also created a load profile from more moderate temperature ranges on Earth, evaluating weather data from Kassel, Beijing and Tromsø.
In the second step, the research team tested the photovoltaic inverter housing in various runs in relation to the temperatures inside and outside the housing. In addition to classic climate chambers, they also used special measuring devices for material characterization for this purpose, such as the TGA-SA, which can be used to continuously measure particularly small amounts of moisture stress by measuring the increase in weight over a long period of time. In order to be able to provide more precise information about the climate inside versus outside the enclosure on the sealing concepts and properties of individual enclosure materials, the climate experts analyzed the corresponding diffusion coefficients. These determine the speed at which moisture penetrates or escapes through a material. The partial water vapor pressure, the humidity and other findings were modeled in the third step, the coupled simulation of temperature and concentration fields using ANSYS® software, thus enabling the representation of the relative humidity and the local temperature distribution in the enclosure. Additional simulations performed on condensation risks, based on the material properties experimentally determined in step two and a day-night cycle with normal and extended holding times, as well as a non-uniform temperature distribution, were also created.
Evaluation of lifetime relevance
Finally, in step four, the test and simulation experts* provide guidance on how cumulative moisture exposure can affect the lifetime of the systems. In the case of the photovoltaic inverter housing, an inhomogeneous temperature distribution occurs due to local dissipation lines and this also leads to an inhomogeneous moisture distribution.
The project over a period of 18 months has shown that the simulation model can predict realistic behavior very well and that Fraunhofer IZM’s test kit makes it possible to clearly investigate the influence of various layout and material optimizations of housings and electronic components. This project can thus now be transferred to diverse electronic components and their housings for the analysis, evaluation and characterization of lifetime relevance and applied already in the early development and conception phase.
This is a novelty especially for production companies of electronic equipment of any kind, because until now failures of electronics were analyzed at most by empirical values, when the electronics had already failed. With the findings of the experts* from Fraunhofer IZM this has come to an end and the documentation of failures can lead simulation and testing before commissioning of the electronic equipment to safer and more durable electronics including their housings.
The project was funded by the ECPE joint research program.
– – – –
Further links
👉 www.izm.fraunhofer.de
👉 Group services
Photo: Fraunhofer IZM