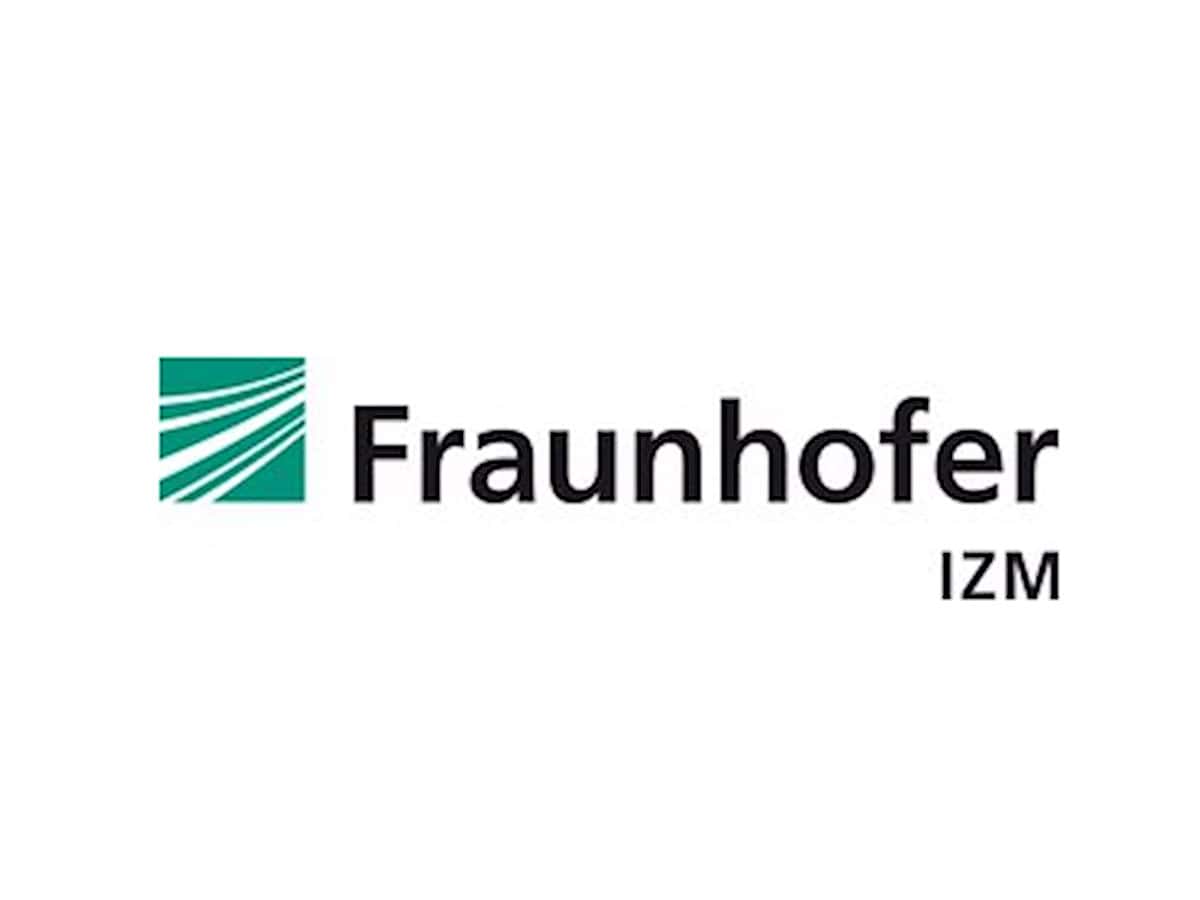
In order to transfer the energy from the battery to the road, the motors of today’s electric cars need an inverter. It is the transformer station in the car, so to speak. The inverter converts the direct current from the battery into what drives today’s motors: three-phase alternating current, commonly known as three-phase current. The higher the power in the drivetrain, the greater the current flow. This increases the likelihood of heat loss. This disruptive side effect is minimized by a new type of converter that Fraunhofer IZM has now developed in collaboration with Porsche and Bosch: the continuous power inverter.
The name says it all, because the continuous power inverter provides almost 600 kilowatts of power, which corresponds to around 815 hp, even over long periods of time. By comparison, this is not only a good one and a half times as much as is currently usual in a 40-ton truck, it also sets new standards in the electrically powered sports car segment. For short-term power peaks, the inverter even achieves values of 720 kilowatts or 979 hp. In order to be able to process such amounts of energy, the development of the continuous power module was based on state-of-the-art semiconductor technology with silicon carbide (SiC) transistors and an innovative cooling system.
High efficiency and low inductance thanks to PCB embedding
The basis for the outstanding performance of the continuous power inverter is the use of silicon carbide (SiC) transistors. A major advantage is the lower module inductance of 1.1 nanohenries – among modules with similar current conductivity, this is absolutely top class. Dominik SeidenstĂĽcker, who played a leading role in this development, explains further advantages: “Compared to conventional silicon transistors, silicon carbide semiconductors are characterized by significantly higher temperature resistance, lower semiconductor capacitances and reduced on-resistance with the same semiconductor surface area. They therefore offer the potential to significantly reduce switching and conduction losses.”
In order to make the system particularly compact, DC-Link capacitors with PolyCharge NanoLam technology were also used. Compared to conventional polypropylene capacitors, they offer more than twice the power density. A special PCB process, in which the semiconductor modules are embedded, further increases system efficiency. Dominik SeidenstĂĽcker comments: “PCB embedding enables us to reduce the distance between the forward and return conductors and thus reduce the leakage inductance. The lower leakage inductance of the module means that we can switch faster. This in turn reduces the losses in the semiconductor once again.” This technology also enables cost-effective mass production. The state-of-the-art design based on SiC technology keeps heat generation in the 12 semiconductor modules installed at a low level. If the continuous power inverter has to transfer particularly large amounts of energy to the drive unit when required, a sophisticated cooling system provides plenty of scope.
Highly modern cooling system from the 3D printer
To ensure that the power electronics can work reliably even under full load conditions, a cooling system was developed that is essentially based on two parts: Firstly, a 3D-printed copper cooling element was developed. “We opted for copper because copper has better thermal conductivity than aluminum and can therefore spread the heat better,” says SeidenstĂĽcker. The element is optimally adapted to the thermal requirements of the components and ensures even heat dissipation. By using silver sintered connections, the temperature-critical components are connected directly to the cooling system, thereby achieving the best possible thermal integration.
The heat is transferred to a water cooling system, the second component of the cooling system. It is manufactured using the aluminum 3D printing process and guides the cooling water through a parallel cooling structure that optimally distributes the pressure in the system. The pressure drop is extremely low at just 150 millibars with 10 liters of coolant per minute – clear proof of the high efficiency of the cooling technology. Even after 15 minutes of continuous load operation, the temperature difference between the housing and the coolant is less than 20 Kelvin. A maximum temperature increase of only 41 Kelvin was measured at the cooled phase output. Thanks to this advanced cooling technology, the inverter remains within the optimum operating temperature range even under high loads. To put it bluntly: even the cooling system stays cool in continuous power.
Maximum power density
The individual components of the continuous power inverter are therefore perfectly coordinated. Their interaction is orchestrated by software that was also developed by Fraunhofer IZM for the project.
Not least, the smart design of the module enables a power pack that sets new standards in terms of power density: At 200 kVA per liter, the inverter delivers two to four times what is common in conventional electric cars. It outperforms today’s top segment by a third. In future, high-performance electric vehicles can therefore be powered by significantly smaller inverters with more power. The continuous power inverter also offers a high degree of modularity: individual components can be replaced or serviced more easily. This saves resources and enables a significantly longer service life for the vehicles.
The combination of state-of-the-art semiconductor technology, optimized cooling and high performance makes the inverter a key component for the next generation of electric drives. The project contributes significantly to the further development of electromobility and raises the bar in terms of performance, efficiency and sustainability.
The project was supported by the German Federal Ministry of Economics and Climate Protection and was carried out in cooperation with Porsche AG and Robert Bosch GmbH.
From May 6-8, Dominik SeidenstĂĽcker will be presenting the continuous power inverter to the public at the Fraunhofer IZM stand (Hall 5, Stand 300) at PCIM Europe. Let our scientists explain the technical innovations to you and take a look at our future-oriented drive inverter with its embedded power modules and the innovative DC link capacitor. Further information about our stand: www.izm.fraunhofer.de/pcim
Technical data
- 3-phase drive inverter
- 48 SiC semiconductors
- approx. 3 l volume of the power core
- 800 or 1200 V base
- Continuous power of almost 600 kW (835 V x 720 ARMS)
- Peak power of 720 kW (800 V x 900 ARMS)
- Power density of 200 kVA per liter
- Peak efficiency of 98,7 %
– – – – – –
Further links
👉 www.izm.fraunhofer.de
Photo: Fraunhofer IZM | Volker Mai