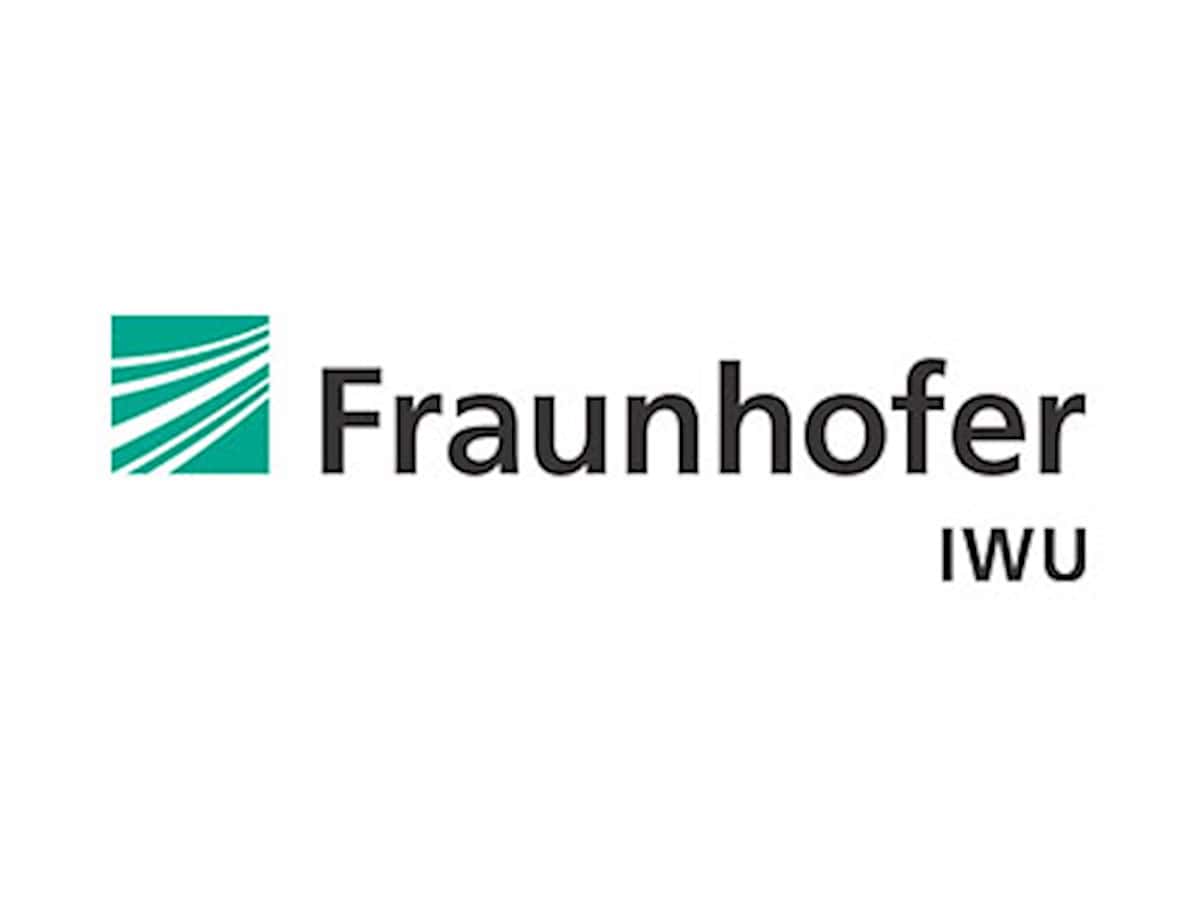
Many small and medium-sized companies are struggling with a shortage of skilled workers and insufficient automation in their production. The consequences are frequent machine downtimes and production errors. Conventional monitoring solutions are often costly and inflexible. This is exactly where ECC4P comes in: The automation solution is flexible, cost-efficient and enables the recording of process data. “Our ECC4P concept reduces rejects, lowers inspection costs and enables continuous production monitoring in a continuous data space with low latency times,” explains project manager Alexander Schuster from the Fraunhofer Institute for Machine Tools and Forming Technology IWU, a specialist in industrial manufacturing.
Complete process control, wear detection and data backup
A central element of ECC4P is the direct recording of sensitive measurement data in the machines. Innovative sensor systems are available for this purpose: smartGRIND for monitoring grinding processes, smartTOOL for milling and drilling processes and smartNOTCH for forming processes. These sensor systems communicate with each other via a specially developed interface. This allows them to be flexibly connected to different evaluation systems or directly to the machine control system. Together with the machine data, the recorded sensor data is transmitted to the ECC4P interface. There, it is fully synchronized before an AI-supported analysis module automatically processes and evaluates the data.
Depending on the application, process anomalies, component rejects or tool wear can be registered at an early stage. The knowledge gained is then fed back to the machine control system so that the machine can react automatically in the event of critical production events. At the same time, the process data and analysis results are stored in a higher-level Edge Cloud. A user-friendly interface makes it easy to retrieve and visualize this measurement and analysis data. They are available on server or cloud instances as well as in the ECC4P cloud. The system thus ensures secure and sovereign data exchange between the edge and the cloud. Changes in the production processes can be intuitively taken into account via a graphical user interface – AI models are automatically adapted and retrained. The computationally intensive training required for this takes place in the cloud, while time-critical processes are processed and evaluated directly on the edge device. Ultimately, production becomes more efficient, safer and more future-proof. The company does not require any costly retrofitting.
ECC4P: Low entry barriers with high security and efficiency
The technology is based on the developments of the Fraunhofer Cluster of Excellence Cognitive Internet Technologies CCIT. It combines edge and cloud computing to create a continuous production and data space. As a result, computing power is distributed according to demand – depending on data volume and latency requirements. The Fraunhofer Institutes for Machine Tools and Forming Technology IWU (Chemnitz), for Integrated Circuits IIS (Erlangen), for Software and Systems Engineering ISST (Dortmund), for Intelligent Analysis and Information Systems IAIS (Bonn) and for Applied and Integrated Security AISEC (Munich) have jointly developed a powerful solution for this. Michael Fritz, Head of the CCIT office in Munich: “With ECC4P, we are paving the way to modern, efficient and future-proof production for SMEs.”
– – – – – –
Further links
👉 www.iwu.fraunhofer.de
Photo: Fraunhofer IWU / Dall-E3