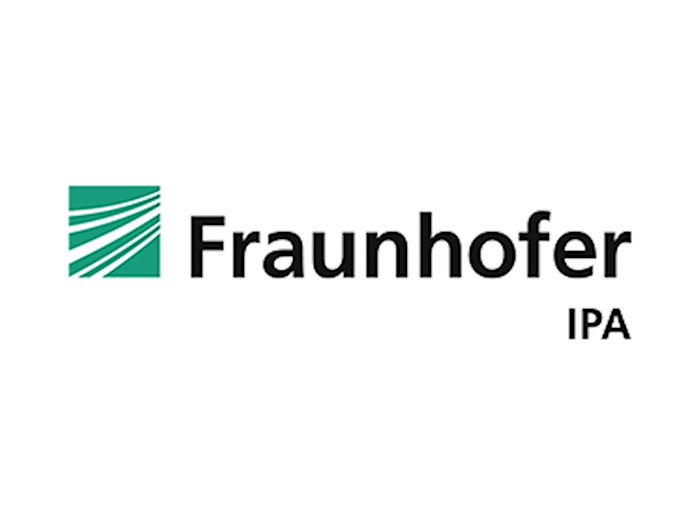
Lead by the company Trumpf, thyssenkrupp Materials Services, the Fraunhofer Institute for Manufacturing Engineering and Automation IPA and other partners are researching how CO2 consumption in sheet metal production can be reduced. The aim is to create a freely accessible online platform that companies can use to accurately determine the CO2 footprint of their component. “Digitization is the key to more climate protection in industry. As a leading supplier and leading user for digitally networked manufacturing, we bring everything we need to make the sheet metal world more sustainable together with our partners,” says Jens Ottnad, project manager at Trumpf. The project started in June and will run for three years. The BMWK is funding it with 8.3 million euros.
Online platform makes emissions consumption transparent
The online platform is intended to make it possible to identify which measures in which production step would bring about the greatest CO2 savings. To this end, Trumpf and thyssenkrupp Materials Services are linking their IT systems to the platform. “To reduce emissions, companies need to know how large their own CO2 footprint is. We want to create the transparency required for this via the online platform. In this way we can simplify the implementation of regulations and also lay the foundation for the circular economy,” says Sebastian Smerat, project manager at thyssenkrupp Materials Services.
Throughout the entire supply chain, the project partners can evaluate measures for greater sustainability thanks to machine and production data. This includes, for example, the concrete CO2 savings when users obtain additional components from a certain amount of metal or avoid unnecessary material transports. “A special feature of de:karb is the reduction of CO2 use through optimizations along the entire value chain. Here, methods of artificial intelligence (AI) and machine learning play a central role,” explains Marco Huber, who is responsible for the project at Fraunhofer IPA.
Technologies around AI and networking
German steel and sheet metal production accounts for around a quarter of industrial emissions in Germany, according to the opening climate protection balance sheet of the Federal Ministry of Economics and Climate Protection (BMWK). It is particularly energy-intensive to produce the raw material. Improving material utilization in production is therefore a focus of the research project. To this end, Trumpf is working on new technologies for nesting in order to cut more parts out of sheet metal with the help of AI.
Another aspect of the initiative is the optimization of the scheduling process, i.e. the timing of production. Here, Fraunhofer IPA is working on using AI to take into account ecological framework conditions in production. For example, it would be possible to allow particularly energy-intensive production steps such as laser processing to take place when as much electricity as possible from renewable resources is available. At the same time, the strategies should ensure users can process orders flexibly.
The task of thyssenkrupp Materials Services is to orchestrate the material, value and data flows by means of a digital platform to be developed. This will make it possible to trace input materials and their characteristics. Uniform standards are to allow networking in the process.
CO2 footprint as a competitive criterion
As the ecological footprint of manufacturing is increasingly becoming a competitive criterion, the partners are already responding to the changing needs of customers and companies with the project. “Especially in Western markets, customers are paying more and more attention to companies’ CO2 emissions. Those who can demonstrate particularly climate-friendly value chains secure competitive advantages,” says Ottnad. Other project partners include the management consultancies AEC and SES-Ingenieure, the Baden-WĂĽrttemberg Cooperative State University, the AI start-up Nash and the sheet metal manufacturer H.P. Kaysser.
Project profile
Full name: de:karb – decarbonizing the manufacturing industry
Funder: German Federal Ministry of Economics and Climate Protection as part of GreenTech Development of digital technologies
Term: 01.06.2023 to 31.05.2026
Project partners: Trumpf (consortium leader), Thyssenkrupp Materials Services, AEC, SES-Ingenieure, Duale Hochschule Baden-WĂĽrttemberg, Nash and H.P. Kaysser
Further links
www.ipa.fraunhofer.de
Photo: TRUMPF