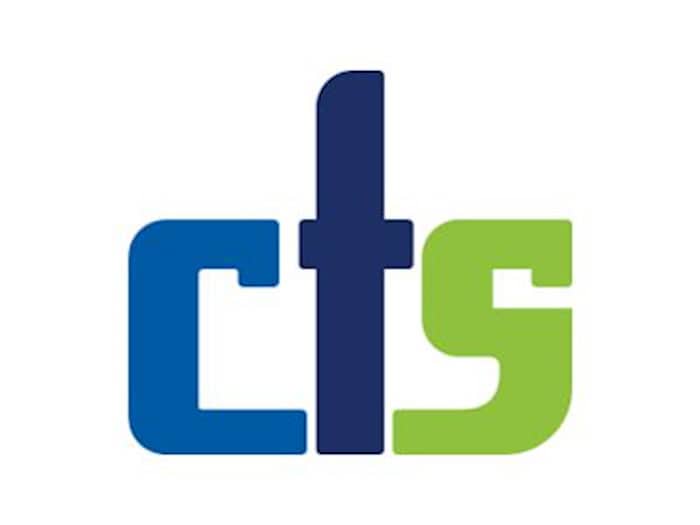
The Smart In-Production Warehouse from CTS has been upgraded: both the Smart Warehouse and its “little brother”, the Mini Smart Warehouse, can now automatically store and retrieve small load carrier (SLC) boxes and tray stacks from various manufacturers, as used in the electronics industry, in addition to PCB magazines. This takes place either in the same area or in an additional, separate area in the warehouse – but always in a space-saving and efficient manner close to the production lines, as they say. As CTS explains, mixed storage brings many advantages for the customer.
“In addition to the PCBs, consumables such as solder paste or cleaning fluid can now also be stored in a space-saving manner and integrated into the fully automated intralogistics system, for example,” explains Alfred Pammer, Head of Sales and Marketing at CTS.
A key basis for seamless material flow monitoring, for example by an ERP system or in the SAP world, is the exact tracking of both the PCB magazines and the KLT boxes, according to Pammer. This is possible with the new storage system. Material is stored and retrieved manually or fully automatically using Autonomous Mobile Robots (AMR), which deliver the material either directly to the production line or to a transfer station.
The containers are identified using RFID chips or DMC/barcodes, for example. Open REST interfaces (Representational State Transfer)/MQTT are available for connection to planning software. According to CTS, the hardware and room layout can be configured according to customer requirements, as can the algorithms for optimizing storage and retrieval. And any browser-enabled end device is sufficient to control the modular storage system, as the company concludes.
Source: MMLogistik
– – – – – –
Further links
👉 www.group-cts.de
Photo: CTS