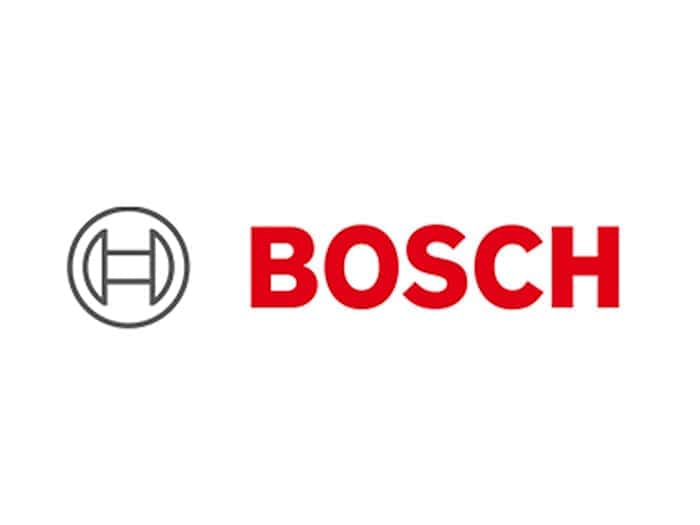
“Bosch remains committed to Germany as a business location and is investing large sums of money here. By introducing new technologies in our plants, we are securing important sales potential,” says Klaus Mäder, member of the Bosch Mobility Sector Board of Management responsible for Operations and therefore all plants worldwide. The new 3D printer is intended to reduce the development cycles for metal parts in particular, which take a long time using conventional manufacturing processes. “With this new acquisition, we are increasing our productivity and speed in the production of metal parts – and therefore our competitiveness,” explains Alexander Weichsel, Commercial Plant Manager in Nuremberg, on the official launch of the system. “We are setting the highest standards in metal 3D printing. This opens up completely new possibilities for us in series production,” adds Jörg Luntz, Technical Plant Manager.
Whether components for hydrogen applications, housings for electric car engines, e-axle components or engine blocks for racing: the sheer size and technical equipment of the system open up numerous applications. Based on a previously developed, computer-aided design file, twelve lasers melt metal powder layer by layer to create highly complex shapes. The new metal 3D printer is up to five times faster than the 3D printing systems previously used. Complex structures such as internal or curved channels, which are simply not feasible with conventional milling processes, can be easily implemented. You can’t drill around corners with conventional methods – but you can with 3D printing. The printer covers the production of the raw parts, without tools and as required. Resources are also conserved, as the waste of raw materials is reduced to almost zero with 3D printing. “Using the 3D printer to manufacture components not only increases sustainability in production, but also enables Bosch to react with great flexibility to volatile quantities and offer everything from a single source,” explains Alexander Weichsel.
Manufacturing a complete engine block using the 3D printing process
The new possibilities of the 3D printing process can be illustrated particularly clearly using the example of an engine block: It can take up to three years from the first draft to series production in conventional production. The completion of the casting mold for the engine block alone can take up to 18 months. This process is no longer necessary with 3D printing. The design data is sent directly to the printer, eliminating the need for complex casting molds. The 3D printer delivers a finished engine block after just a few days, significantly reducing the development time for the entire product.
Under full load, the system can produce metal parts with a total weight of around 10,000 kilograms within a year, achieving speeds of up to 1,000 cubic centimetres per hour. In particular, the faster production of components should shorten the time to market. “We want to pick up speed compared to the traditional manufacturing process and bring products to market faster with this new technology,” says Jörg Luntz. “Even today, only a few companies can produce technology on an industrial scale like Bosch. We are now taking the next step and bringing series production in metal 3D printing up to automotive level.” This opens up completely new opportunities and possibilities – in the automotive sector, but also in numerous other industries such as the energy or aviation sector.
Whether components for hydrogen applications, housings for electric car engines, e-axle components or engine blocks for racing: the sheer size and technical equipment of the system open up numerous applications. Based on a previously developed, computer-aided design file, twelve lasers melt metal powder layer by layer to create highly complex shapes. The new metal 3D printer is up to five times faster than the 3D printing systems previously used. Complex structures such as internal or curved channels, which are simply not feasible with conventional milling processes, can be easily implemented. You can’t drill around corners with conventional methods – but you can with 3D printing. The printer covers the production of the raw parts, without tools and as required. Resources are also conserved, as the waste of raw materials is reduced to almost zero with 3D printing. “Using the 3D printer to manufacture components not only increases sustainability in production, but also enables Bosch to react with great flexibility to volatile quantities and offer everything from a single source,” explains Alexander Weichsel.
Manufacturing a complete engine block using the 3D printing process
The new possibilities of the 3D printing process can be illustrated particularly clearly using the example of an engine block: It can take up to three years from the first draft to series production in conventional production. The completion of the casting mold for the engine block alone can take up to 18 months. This process is no longer necessary with 3D printing. The design data is sent directly to the printer, eliminating the need for complex casting molds. The 3D printer delivers a finished engine block after just a few days, significantly reducing the development time for the entire product.
Under full load, the system can produce metal parts with a total weight of around 10,000 kilograms within a year, achieving speeds of up to 1,000 cubic centimetres per hour. In particular, the faster production of components should shorten the time to market. “We want to pick up speed compared to the traditional manufacturing process and bring products to market faster with this new technology,” says Jörg Luntz. “Even today, only a few companies can produce technology on an industrial scale like Bosch. We are now taking the next step and bringing series production in metal 3D printing up to automotive level.” This opens up completely new opportunities and possibilities – in the automotive sector, but also in numerous other industries such as the energy and aerospace sectors.
– – – – – –
Further links
👉 www.bosch.de
Photo: Bosch