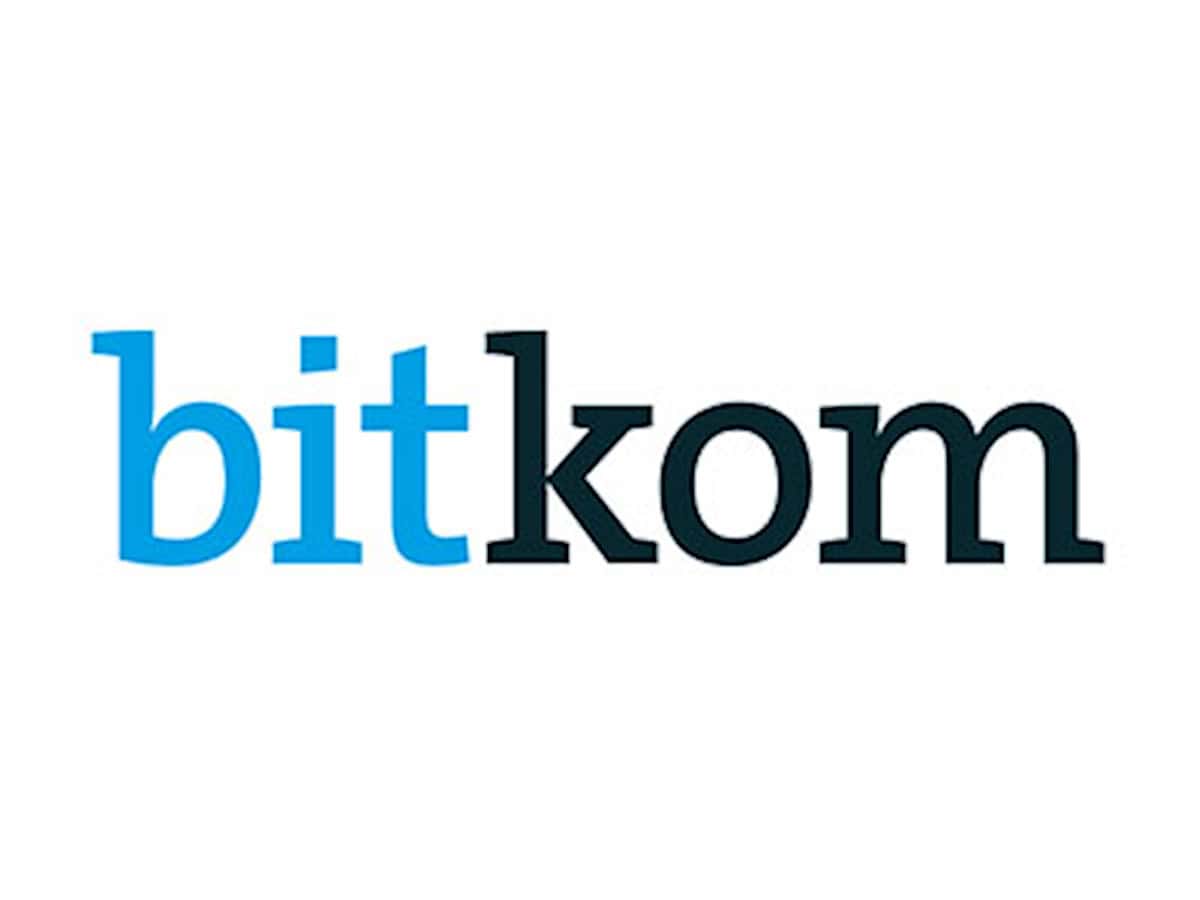
According to the survey, the vast majority of companies are in favor of intensifying AI efforts in the industry: More than three quarters of companies call for German industry to take on a pioneering role in the use of AI (79 percent). However, not everyone is convinced: just under a fifth believe that AI in industry is just a temporary hype (21%). “In view of geopolitical tensions, international trade conflicts and the economic crisis in Germany, we need to improve our competitiveness and strengthen our technological independence. This can only be achieved through digitalization,” says Bitkom Vice President Christina Raab. “An investment in a key technology such as artificial intelligence is therefore not just a cost factor, but an essential part of a sustainable strategy.”
Artificial intelligence is currently most frequently used in analytics, for example to monitor the functionality of machines – 32% of companies use AI for this purpose, with a further 42% planning or discussing this. One in five companies (19%) uses AI in robotics, with 46% planning or discussing this. Energy management offers the greatest potential for the future: although AI applications are only being used by 7% of companies, around two thirds of companies are planning or discussing this (64%).
What obstacles are there to the introduction of AI applications? 42 percent report a lack of expertise in integrating AI into existing processes. And half (50 percent) are waiting to see what experiences others have had with the use of AI. “Artificial intelligence is becoming a basic technology in industry. Companies should therefore integrate AI skills into the training and further education of all employees,” says Raab.
Industry 4.0 as an opportunity in international competition
For 8 out of 10 industrial companies (81 percent), Industry 4.0 applications, i.e. the use of digitally networked technologies in production, represent an opportunity. Such technologies are currently being used by 7 out of 10 industrial companies in Germany (71 percent) – and a further fifth (21 percent) are in the planning stage. Only 5 percent of companies state that they do not yet have any plans – but that an entry into Industry 4.0 is certainly conceivable. One reason for this hesitation is a lack of time. 8 out of 10 companies (81%) that can imagine using Industry 4.0 but are not yet planning to do so do not have the time to deal with it. Companies for which Industry 4.0 is not an issue at all do not actually exist. And all companies that have introduced Industry 4.0 applications have stuck with it, no one has turned back the clock. This is because Industry 4.0 strengthens their own economic situation and competitive position: almost all companies consider it indispensable in order to survive in international competition (96 percent) – and among those already using corresponding applications, it is currently helping a third (33 percent) in the economic crisis.
What is the mood in German industry? Overall, almost half of companies (46%) see their own existence threatened by the current economic situation – and digitalization is also suffering as a result. This is because 4 out of 10 companies (42%) expect their own digitalization to be slowed down by the economic situation. Geopolitical developments are not sparing German industry either: almost 7 in 10 companies (68%) are convinced that Donald Trump’s presidency will harm German industry. One possible reason for this is new and rising tariffs – to which 43% of industrial companies would even respond by relocating production. “Geopolitical uncertainties, rising tariffs or the dependence on technologies from abroad can have a massive negative impact on German industry. Targeted investment in key technologies such as AI or data rooms not only ensures competitiveness, it also strengthens the resilience and technological sovereignty of German industry,” says Raab.
IoT, digital twins, metaverse & Co.: numerous other applications in planning
Despite everything, major investments are in sight for the near future: despite the recession, on average, the same amount or more will be invested in Industry 4.0 this year than in the previous year. Compared to 2024, only around one sixth (17%) of industrial companies plan to reduce investment in Industry 4.0, while around one third (36%) plan to increase it: Just under a quarter intend to invest more (23 percent), while 13 percent plan to invest significantly more. 44% want to keep their investment volume for 2025 stable at the same level as in 2024. “Digitalization does not come for free – the majority of industrial companies have realized this,” says Raab.
German companies are relying on a wide range of different technologies. IoT platforms are currently emerging as the frontrunners for the future. Such solutions, which connect products, machines, processes and people, are already being used by 46% of companies, and almost as many (43%) are planning to do so. Digital marketplaces, which make it easier for industrial companies to exchange goods and services, for example, are the most widespread. They are already used by over half (53%) of companies. Digital twins, i.e. virtual models of processes, products or entire production facilities, are also increasingly being used: almost half (48%) of German industrial companies state that they use such applications. Additive manufacturing, also known as 3D printing, is currently used by four out of ten (43%), while virtual or augmented reality is used by a third (33%). Edge computing and data rooms (28% each) and lifecycle management (27%) are currently still the least common – however, the spread of data rooms has already picked up speed in the last three years with an increase of 8 percentage points (2022: 20%).
Manufacturing-X kicks off in Germany
Interest in data rooms is also growing – they are used to exchange information between different companies. The cross-industry Manufacturing-X initiative aims to connect the manufacturing industry and its supply chains through such a data room in Europe. Participation in this initiative is now underway: One in twenty German companies (5 percent) is already participating, while 8 percent are planning to do so. Around a third (31%) of companies can at least imagine participating. However, just under half (48 percent) have not yet looked into Manufacturing-X enough to consider participating. Only 5 percent have consciously decided against it at this point.
The digital exchange of data has many advantages, however – German industry also sees this: over half of companies (56 percent) see a positive effect on the resilience of German industry, and almost half (48 percent) also believe that the digital exchange of data contributes to the technological sovereignty of German industry. And digital exchange is also crucial for competitiveness, according to 48%. However, 4 out of 10 companies (40 percent) say that this digital data exchange is still too complicated for their company.
In international comparison in third place for Industry 4.0
When it comes to Germany’s position in an international comparison of Industry 4.0, companies are divided. Just under half (49%) see Germany as a latecomer, while almost a quarter (23%) even say that Germany has missed the boat when it comes to Industry 4.0. Conversely, however, a quarter (26 percent) also see Germany in the lead: one in ten companies place Germany at the top internationally (9 percent), while 17 percent describe it as a pioneer.
China is most frequently placed in pole position worldwide. A quarter of German industrial companies (26 percent) consider the country to be the frontrunner when it comes to Industry 4.0. The USA is in second place, with 23 percent of companies seeing it as the most progressive nation. Germany is in third place (12 percent). Japan is in fourth place with 9 percent, followed by South Korea (7 percent).
How do you become a pioneer in Industry 4.0? Obviously, the companies themselves have it in their own hands: the greatest importance is attached to a high level of interest on the part of industry. 6 out of 10 companies that regard a nation as a leader consider this to be decisive (57 percent). This is followed by a more favorable legal framework, which around half see as a success factor (52 percent). A pioneering role in establishing standards (29%), high investment in research and development (27%) and strong political support (18%) continue to be important. “The industry sees the framework conditions in countries such as China and the USA as more advantageous. Germany invests heavily in research and development, but otherwise has some catching up to do. We can take our lead from other players: According to German industry, South Korea offers favorable legal conditions, while the USA is convincing when it comes to standards,” says Raab.
Need for action in regulation, but also among companies themselves
How can industrial companies be better supported in the introduction of Industry 4.0 applications? First of all, legal uncertainties need to be removed so that data can be exchanged more easily with other companies, say 86 percent of industrial companies. 4 out of 10 (40 percent) are of the opinion that the establishment of standards for Industry 4.0 applications would be helpful. With regard to AI innovations, almost 9 out of 10 companies (88%) also demand that politicians should not stifle them through over-regulation.
Financial support would also be helpful: three quarters of companies (78%) see tax incentives as beneficial, while two thirds (66%) would like to see funding applications approved more quickly. Three quarters of industrial companies (76%) consider better broadband expansion to be useful in order to ensure reliable data exchange between machines. Another factor that should not be neglected is education: In times of a significant shortage of skilled workers, 6 out of 10 companies (59 percent) consider education and training programs for skilled workers in the field of Industry 4.0 to be beneficial.
– – – – – –
Further links
👉 www.bitkom.org
Graphic: Bitkom