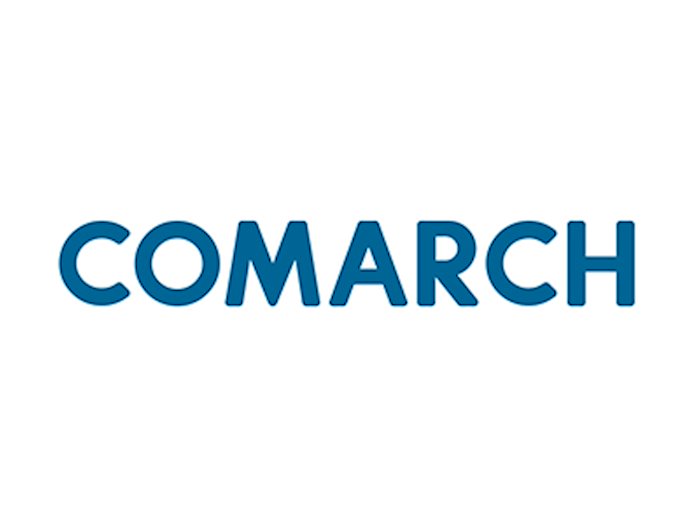
The automation of production processes in a company should begin with a theoretically simple, but strategically very advanced adaptation of the management itself. Here we are referring to the concept of lean management, which is based on flowing and optimized production and the pull principle, among other things.
What is lean management – simply explained
The beginnings of lean management can be traced back to Japanese organizations, in particular the Toyota production system. The lean concept is also well suited to pure production processes (lean manufacturing), making it easy to track the consumption of resources by a company and avoid waste of any kind on the production line. Lean management methods are therefore ideal for companies of all kinds and for companies and types of production that see their priority not only in increasing their potential, but also in sustainability.
Concepts of the lean philosophy
The lean philosophy is based on a series of concepts that aim to minimize waste, increase efficiency and improve quality.
These concepts are essential for understanding and successfully implementing the lean philosophy in companies and organizations. They play a crucial role in reducing costs and increasing customer satisfaction. The key concepts of the lean philosophy are listed below:
Muda or waste
The term “muda”, which is borrowed from the Japanese language and means nothing other than superfluous, is used in lean management concepts. Anything that is superfluous can be directly correlated with losses or waste that needs to be avoided in automated production. Typically, seven types of “muda” are distinguished, for which we at Comarch have developed our own answers.
– Overproduction. An IoT-based MES system, for example, can help you to control this by managing orders and tracking their processing. The operator always has the most important variables available, including the number of units already produced and those still to be produced.
– Excessive stocks lead to disorganization in the warehouse and do not allow materials to be used effectively. To optimize warehouse operations, a real-time location system (RTLS) should be used. This is the only way to always know where products are located and what stock quantity is available. Ultra-wideband technology (UWB), for example, is ideal for the most precise tracking possible.
– Quality errors and defects are checked for you by the Comarch IoT MES app. With the help of our quality inspection module, you can control all processes even better by checking the quality after each step and not only after the entire workpiece has been completed. With its help, errors and defects can be detected and rectified as quickly as possible.
– The real-time information flow shortens waiting times. No more material on the production line? Press a special display button or the dedicated Comarch Smart Button. This requests the provision of material for production. The system can be used to track the progress of work, so you can prepare material for the next production stages before a process is completed.
– Superfluous transportation can be avoided quickly and effectively with the help of Asset Tracking. With the help of this tool, you can localize the locations of your production equipment in real time and track its movements. The tool is ideally suited to the digitalization of intralogistics processes.
– The use of innovative software can reveal waste in process flows, which can eliminate unnecessary movements.
Mura or deviation or imbalance
Another concept of lean management is Mura. Irregularities (Japanese mura) in the processes to be carried out can also lead to damage, from cost fluctuations to quality fluctuations. The Internet of Things and MES solutions are used to sort the work correctly by storing and evaluating all production and product quality parameters in a database. The work instructions provided to production personnel also improve the quality of performance.
Muri or overload
Overload (Japanese muri) due to severe operating conditions can affect people as well as machines or systems. Overload can occur, for example, as a result of too many duties being imposed or production facilities being overloaded compared to the existing operating conditions, ultimately leading to malfunctions and accidents. Continuous monitoring of the time and utilization of machines can prevent overloading and optimize the entire production process as well as the automation of production or automation of manufacturing.
Automation production based on the lean method allows to optimize all processes and procedures taking place in a company, as well as to minimize or even completely eliminate waste. If you are ready to take your first steps towards digitalization, read more about Comarch’s solutions for Industry 4.0.
Tools and methods of lean management
There are many tools available in the manufacturing industry to successfully implement lean management principles. The key is to select the tools that best suit the individual context of a company. At the same time, the definition and introduction of key performance indicators (KPIs) is of great importance in order to measure the results achieved. This ensures continuous monitoring and adjustment of measures if necessary. Companies can thus develop a customized lean management strategy and embark on the path to continuous improvement.
Kanban
Kanban is a visual material flow management system that enables the just-in-time provision of materials by displaying current demand in real time and only triggering reorders when materials are running low. This method aims to reduce stock levels to the quantities actually required, which helps to increase efficiency in the production chain.
Value stream mapping
Value stream mapping aims to quickly identify waste in successive production processes and uncover optimization potential. All process steps are recorded and analyzed for this purpose. The method begins by recording the current status of the processes in order to identify weak points and potential for improvement. The processes are then redesigned to create a more efficient and waste-free production chain. The value stream analysis visualizes the entire production flow, which makes it possible to identify bottlenecks and inefficient steps. This leads to better process optimization and shorter throughput times, which makes production processes considerably more efficient.
Just-in-time (JTI)
JIT is a concept of lean production in which materials are only delivered when they are needed for production – and in exact quantities. The aim of the JTI strategy is to design the material flow in such a way that it is synchronized with the production process. This reduces stock levels, lowers warehousing costs and increases responsiveness to customer orders. The entire value chain is therefore simpler and processes are streamlined.
5S method
The 5S method is a systematic approach to designing your own working environment in such a way that non-value-adding activities, i.e. waste, are reduced. The method is based on five steps that all begin with an “S” (Sort, Systematize, Clean, Standardize, Self-discipline) and promotes the reorganization and improvement of clean, safe and standardized workplaces.
Kaizen
Kaizen describes a methodical concept aimed at continuous improvement. The principle of the continuous improvement process is intended to lead to improved quality management and process optimization in the long term. It encourages employees to constantly look for ways to permanently improve workflows, processes and products. The method is based on the idea that small, incremental changes or improvements have a significant impact over time.
Implementing lean management in manufacturing companies
Implementing lean management in manufacturing companies is a comprehensive process and ideally begins with strong management commitment and engagement. This is followed by the comprehensive training of all employees at various levels, including management, to familiarize them with the basics of lean management.
After the basic awareness and training of all employees, including management, the next step is the concrete implementation of lean management methods. As already described in the section ‘Tools and methods of lean management’, these methods are introduced in order to enable gradual integration into company practice.
Visualization plays an important role here in order to clearly record work progress and performance. The involvement of employees should not be missing. Greater success is achieved when employees at all levels are involved in the improvement process and motivated to contribute their own ideas to increase efficiency. To ensure that lean measures achieve the desired goals and results, performance must be continuously measured and evaluated. Lean methods are gradually adapted and can be extended to other areas of the company. This sustainably increases the overall value for the company.
Lean management and Industry 4.0 – the benefits
The interplay between lean management and Industry 4.0 has a number of advantages for companies, as it can increase efficiency, flexibility and competitiveness. Below are some of the outstanding benefits of this synergy:
Increased efficiency
Lean management aims to minimize waste and optimize processes, while Industry 4.0 uses technologies such as the Internet of Things (IoT), machine learning and big data analytics to collect and use data in real time. The combination enables even more accurate monitoring and control of manufacturing processes, leading to a significant increase in efficiency.
Cost reduction
By identifying and eliminating waste and optimizing processes, companies can already achieve cost savings with lean management. When these approaches are combined with Industry 4.0 technologies, companies can realize even greater cost benefits as they can deploy their resources even more efficiently.
Real-time data and analytics
Industry 4.0 enables the collection and analysis of real-time data from the entire production chain. This data provides valuable insights into the status of production and makes it possible to react immediately to deviations or problems. This helps to improve quality and avoid waste.
Inventory management
The combination of lean management and Industry 4.0 enables more accurate monitoring and management of stock levels. Companies can reduce inventory costs by better predicting demand and optimizing just-in-time deliveries.
Flexibility and adaptability
Industry 4.0 technologies enable companies to make their manufacturing processes more flexible and adaptable. Lean management helps to use this flexibility to adapt production to current requirements and respond quickly to changes in demand.
Quality improvement
Continuous monitoring and analysis of production data enables companies to identify and rectify quality problems at an early stage. This leads to an improvement in product quality and a reduction in waste.
Customer focus
The combination of lean management and Industry 4.0 enables companies to respond even better to the needs of their customers. By closely tracking customer orders and requests, products can be customized and delivery times can be shortened.
Competitive advantage
Companies that successfully combine lean management and Industry 4.0 can gain a competitive advantage by being more efficient, flexible and customer-oriented.
The synergy of lean management and Industry 4.0 synergy thus offers a powerful union to strengthen the competitiveness of companies in an increasingly digitalized world and to optimize their production processes.
Lean Management vs. Lean Production
Lean Management and Lean Production are two terms that are closely linked and often used interchangeably, but they refer to different aspects of the Lean approach to optimizing business and manufacturing processes. The main differences between lean management and lean production are explained below:
Lean production
The focus of lean production is on manufacturing. Lean production mainly concentrates on optimizing production processes and eliminating waste (muda) in production. It was originally developed in the automotive industry, particularly at Toyota, and emphasizes reducing inventory, increasing productivity and ensuring quality.
Division-specific: Lean production is primarily focused on physical production and the associated processes. It deals with aspects such as improving production flow, just-in-time delivery of materials and minimizing waste.
Typical tools and techniques of lean production to optimize processes and reduce waste are methods already described above such as value stream mapping, Kanban, 5S and Kaizen.
Lean management
Holistic approach: Lean management goes beyond pure production and extends to the entire company. It aims to create a lean culture that focuses on continuous improvement, customer satisfaction and employee engagement.
Includes more than just manufacturing: Lean management can be applied across multiple industries and departments, including sales, marketing, procurement, finance and more. It strives to reduce waste and inefficiency in all areas of the business.
Behavior change: Lean management requires a change in the company culture and management system to promote continuous improvement and open communication. It emphasizes the active involvement of employees at all levels.
Strategic alignment: Lean management also includes strategic elements such as aligning business objectives with customer requirements, creating value for customers and identifying competitive advantages.
In practice, lean production and lean management are often closely linked. Lean management sets the strategic framework and promotes the lean culture, while lean production provides specific tools and methods for process optimization. Together, they strive to make companies more efficient, flexible and customer-oriented.
Lean Management vs. Lean Production: The interplay with Industry 4.0
Lean Management and Lean Production are approaches to increasing efficiency and eliminating waste, while Industry 4.0 focuses on digitalization and networking in manufacturing. These approaches can be combined to optimize manufacturing processes in an increasingly digital and automated environment. The following explains some of the connections:
Digitalization and data analysis
Industry 4.0 involves the use of IoT (Internet of Things), sensors and big data analysis to collect real-time data from production. Lean management can use this data to identify and improve bottlenecks, waste and efficiency issues.
Automation and flexible production
In Industry 4.0, the automation of manufacturing processes and the implementation of cyber-physical systems (CPS) also play an important role. Lean production can use automation to further reduce waste and make production more flexible.
Real-time transparency
Both approaches strive for real-time transparency in production. Industry 4.0 makes this possible by networking machines and systems, while lean management relies on methods such as value stream mapping and visualization to track and optimize processes.
Customer focus
Both lean and Industry 4.0 focus on customer satisfaction. Lean management emphasizes the alignment of all activities with customer value, while Industry 4.0 enables the production of individualized products on a large scale.
Continuous improvement
Lean management is based on the idea of continuous improvement. In conjunction with Industry 4.0, companies can quickly access real-time data and integrate permanent improvements into their digital processes.
Adaptability and flexibility
Both approaches offer the ability to quickly adapt to changing market conditions. Lean production enables lean production, while Industry 4.0 enables flexibility through intelligent manufacturing.
Resource efficiency
In addition, both approaches aim to use resources efficiently. Lean management focuses on reducing waste, while Industry 4.0 uses data and automation to optimize energy and materials.
The interaction of lean management, lean production and Industry 4.0 can significantly increase a company’s competitiveness by enabling efficient, flexible and customer-oriented production. However, this requires careful planning, investment in the appropriate technology and a change in corporate culture towards continuous improvement and digitalization.
– – – – – –
Further links
👉 www.comarch.de
👉 Efficient data-supported digitalization of production
Photo: Comarch