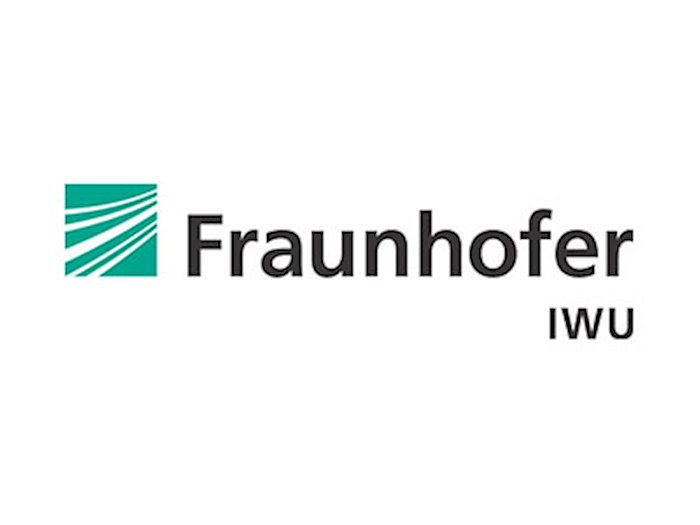
Quality predictions
Typical future areas of application for the newly developed AI solution are machining steps such as drilling, turning and milling. In drilling, for example, speed, feed rate and measurements by a vibration sensor provide information about the expected qualitative result. This makes it possible, for example, to obtain a quality statement for deep-hole drilling without having to destroy the workpiece for a measurement.
Process optimization
In the area of metalworking, the use of AI has proven itself not least in hot forming. In this process, the workpiece is heated above the austenitizing temperature (approx. 880 °C) in the furnace before pressing. As soon as the desired target temperature for optimum hardening results is reached, the hot sheet is inserted into the press by a handling system and formed. A martensitic structure is formed, and the material is thus hardened. Since product quality is the primary concern in this energy-intensive process, the furnace temperature is often set higher than it should be. By predicting the foreseeable hardness, the AI provides data-based assistance for fine-tuning the hardening temperature.
In injection molding processes, the AI monitors specific parameters such as the temperature of the mold, the rotation speed of the screw conveyor for the granules, the melt temperature, the holding time of the mold and the cooling time. Timely countermeasures in the event of an unfavorable quality forecast thus help to significantly reduce scrap.
100% inspections, low number of training data sets
In all application scenarios, the AI can be used directly in the manufacturing process (inline) to monitor the entire batch (100% inspections). Sole random checks are a thing of the past.
For training different AI models, a two-digit number of data sets is sufficient in many applications, supplemented by expert knowledge of the process. In operation, the computing power of (local) edge computing is often sufficient.
Jointly with Synapticon GmbH: Fraunhofer IWU presents new architecture for human-robot collaboration (MRC)
For robots intended for MRC (cobots), particularly high requirements apply to the safety of the motion sequences: the central safety module must process data from numerous sensors, which requires many cable connections for sensors and actuators in traditional robot architectures and proprietary solutions. The new safety architecture developed by Fraunhofer IWU, NexCOBOT and Synapticon GmbH is designed in a decentralized manner; it enables safe interaction between humans and industrial robots even when work situations change dynamically – with significantly reduced cabling requirements. Only power and communication connections need to be routed to the drives. Another advantage: Since the safety of the motion sequences is monitored directly at the drive axis, significantly less reaction time is required. At Automatica, the new solution can be seen at the Synapticon GmbH booth.
Further links
www.ipa.fraunhofer.de
Photo: Fraunhofer IWU