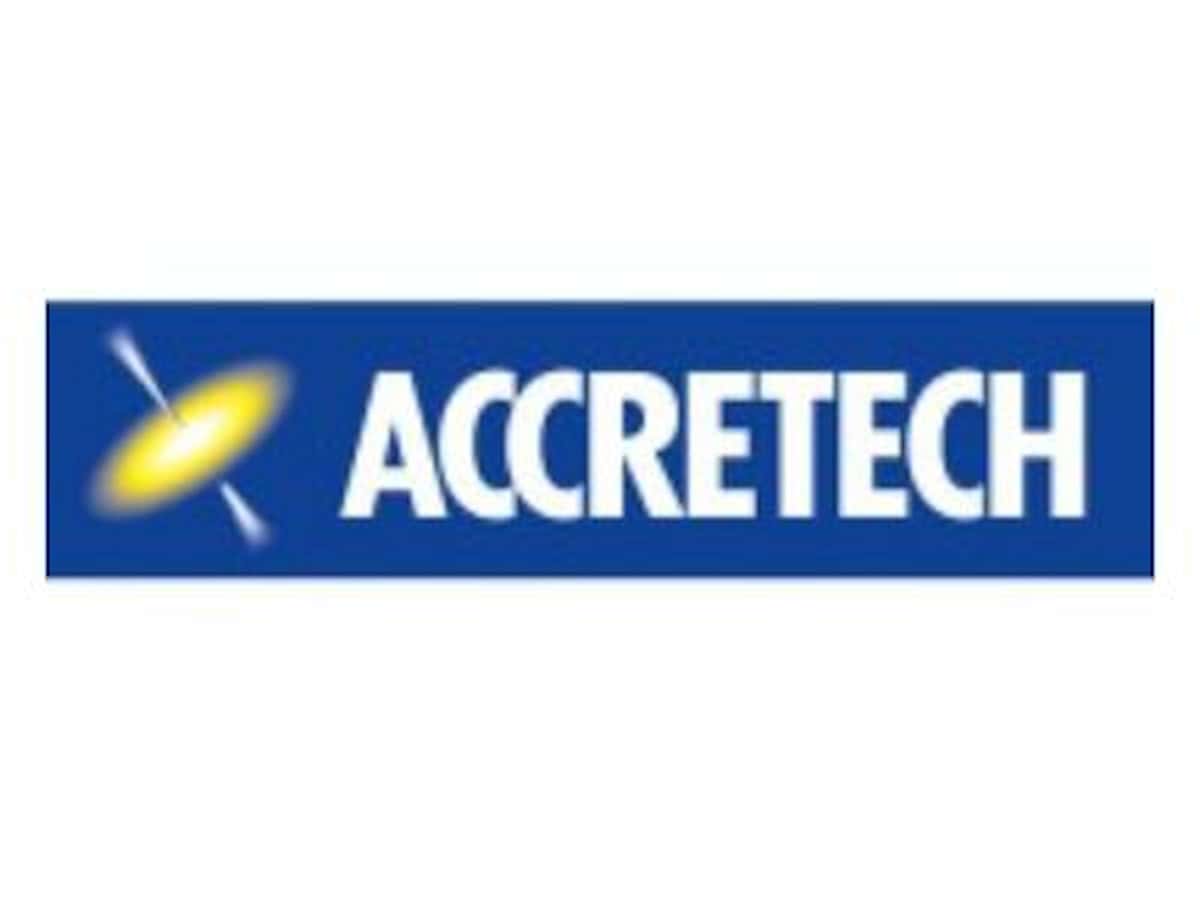
Haie gehören zu den schnellsten Schwimmern überhaupt. Bis zu 70 km/h können die Knorpelfische unter Wasser erreichen. Möglich macht das unter anderem die Beschaffenheit ihrer Haut. Die nämlich besteht aus Schuppen mit einer Rillenstruktur, die den Strömungswiderstand reduziert.
Die Erkenntnis ist nicht neu. Doch das Übertragen auf Flugzeuge stellt eine echte Innovation dar. Fünf bis sechs Jahre flossen bei der BASF Coatings in die Entwicklung der SharkSkin, die den Luftwiderstand reduziert, Treibstoff und damit Kohlendioxidemissionen einspart. Versuche in Windkanal, Computersimulationen und -tests rund um den Rumpf der betreffenden Flugzeugmodelle lieferten tiefgreifende Erkenntnisse zu Aerodynamik und Strömungsverhältnissen sowie den Anforderungen an die SharkSkin und ihre Ausrichtung am Flugzeug. Ergebnis ist eine selbstklebende Folie, die eine Rippen- oder auch „Riblet“- Struktur aufweist. Die Riblets messen in der Höhe etwa so viel wie der Durchmesser eines menschlichen Haars. Mit dem bloßen Auge kaum zu erkennen, mit dem Fingernagel jedoch spürbar. Grundsätzlich lassen sich Riblets überall dort einsetzen, wo turbulente Strömungen herrschen. Beispielsweise an Zügen, Schiffen, Automobilen, Windkraftanlagen, etc. Dank des neuen Produkts konnte sich die Coatings-Division 2024 den BASF Innovationsaward sichern.
Bei der Produktion in Münster werden die Riblets auf eine Trägerfolie aufgebracht. Auf der Oberseite schützt eine weitere Schicht die Struktur und auf der Unterseite bereitet eine Klebefolie die SharkSkin auf ihren Einsatz am Flugzeug vor. Rund 800 Quadratmeter sind nötig, um einen kompletten Rumpf zu folieren. Beim Bekleben des Flugzeugs müssen sich die Werker penibel an das Schnittmuster halten, bevor sie die rund einen mal einen halben Meter großen Patches schneiden und sorgfältig von Hand per Gummirakel auf den Rumpf der Maschinen kleben. Denn nicht überall sind die Anströmwinkel gleich. Ein im falschen Winkel angebrachtes Patch etwa könnte den Verbrauch steigern statt senken.
Das Ergebnis kann sich sehen lassen: Bis dato hat eine global bekannte Fluggesellschaft insgesamt 25 Maschinen der Typen Boeing 777 und 747 in Linien- und Frachtdienst mit der SharkSkin ausgestattet und spart damit etwa ein Prozent Kerosin ein. Bei einem Transatlantikflug zwischen Deutschland und den USA beispielsweise fließen so 1,5 Tonnen weniger Treibstoff durch die Triebwerke. Das reduziert die Emission des Klimakillers CO2 um stattliche 4,7 Tonnen auf nur einem Flug. Allein die 12 Boeing 777 der SWISS seien mit der „Haut“ in der Lage, jährlich 15.000 Tonnen Kerosin einzusparen, rechnet Patrick Scherrer, Projektleiter bei SWISS vor. Das entspricht einem Quantum, das für 87 Flüge zwischen Zürich und Mumbai in Indien nötig wäre.
Im Betrieb ist die Folie extremen Belastungen ausgesetzt. Nicht nur Staub, Sand, Wasser und Enteisungsmittel muss die SharkSkin widerstehen. Auch die enorme UV-Einstrahlung darf der Folie nichts anhaben können. Die Deformierung des Rumpfes im Flugbetrieb erfordert obendrein ausreichende Flexibilität. Zudem muss die Folie den hohen Temperaturunterschieden zwischen Boden und Flughöhe trotzen. Der Start erfolgt beispielsweise in einem Wüstenstaat bei 50 Grad, auf Reisehöhe ist der Rumpf Temperaturen von rund -60 Grad Celsius ausgesetzt – und das bei zirka 900 km/h.
Da die Folie in die Aerodynamik der Flugzeuge eingreift, musste in Tests die Widerstandsfähigkeit der SharkSkin nachgewiesen werden, um eine Zulassung für die Verwendung an den Boeing-Modellen zu erhalten. Ziel ist nun die Freigabe für weitere Flugzeugtypen sowie die Verwendung der Folie an den Tragflächen. Das wird einen weiteren Quantensprung bedeuten und das Einsparpotential der SharkSkin auf das Niveau der „Winglets“ heben – jener vertikalen Fortsätze am Ende der meisten Tragflächen von Verkehrsflugzeugen. Und die reduzieren Verbrauch und Emission um gut drei Prozent.
Selbstredend bedarf es regelmäßiger Überprüfung der Folie an den Maschinen auf Beschädigung und Verschleiß. Den Zustand der Riblets mit bloßem Auge zu kontrollieren, ist freilich nicht möglich. Obendrein stellt sich bei einer solchen Prüfung stets die Herausforderung, dass sie an allen Stellen des Flugzeugrumpfs stattfinden können muss – auch in der Senkrechten oder gar über Kopf. Sperrige und schwere Messgeräte scheiden dabei also von vornherein aus. Daher setzt BASF Coatings auf das zuverlässige, genaue und universal einsetzbare Oberflächenmessgerät HANDYSURF+ des renommierten Messmittelspezialisten ACCRETECH. Bei BASF ist das kompakte, tragbare Gerät bereits seit 2020 erfolgreich im Einsatz.
Marc Daniel von der Abteilung Technical Development Aviation bei BASF Coatings zeigt sich überzeugt vom HANDYSURF+. „Das Gerät ist immer und überall einsatzbereit, sehr einfach zu bedienen und misst äußerst genau“, so der Techniker. Im konkreten Einsatzbereich wird die Rauheitsmessung als Mass der Qualität der Riblets genutzt.
Das HANDYSURF+ verfügt über einen Messbereich von 370 μm auf der Z-Achse – den größten seiner Klasse – und erzielt eine Auflösung von 0,0007 μm über den gesamten Messbereich hinweg. Zum Lieferumfang gehört obendrein das Excel Makro „SupportWareII“, das es ermöglicht die Auswertung in ein Protokoll auszugeben. Der Nutzer hat die Wahl zwischen mit Tastspitzen 2µm und 5µm. Obendrein liefert ACCRETECH das Gerät mit einem Raunormal mit zwei Messflächen inklusive Zertifikat, einer Kunststoffablage, um das Messgerät zum Raunormal korrekt zu positionieren, einer CD mit Anleitung und SupportWareII sowie einem Transportkoffer.
BASF Coatings nutzt zudem die optionale Software ACCTee, mit der sich Messpunkte einfach und schnell einlesen und analysieren lassen – mit einem Modul für Rauheitsauswertung sowie einem weiteren zum Messen von Konturen.
Bei einem Testlauf mit Geräten unterschiedlicher Anbieter hat sich das ACCRETECH HANDYSURF+ als das Beste für den Einsatzzweck herauskristallisiert. Und obendrein kommt das Gerät auch in der Qualitätssicherung der SharkSkin-Produktion zum Einsatz. So entpuppt sich das HANDYSURF+ als Allzweckwaffe rund um die High-Tech-Folie. Und ACCRETECH leistet so einen Beitrag zu Klimaschutz und einer nachhaltigeren Zukunft.
Kontakt
ACCRETECH (Europe) GmbH
Ralph Girardello
Landsberger Straße 396
81241 Munich
Germany
Phone +49 89 250064200
– – – – –
Weiterführende Links
👉 www.accretech.eu
👉 Mehr Informationen zu unserem HANDYSURF+
Foto: ACCRETECH